The Caswell Cove condominium complex in Milford, Conn., is a peaceful coastal gem. Situated on the banks of the Housatonic River, it offers waterfront vistas, access to an adjacent private marina, and magnificent sunset views. But while the setting is spectacular, it was no friend to the complex’s seven 25-year-old EPDM roofs.
The salt-laden spray coming off the brackish river, hurricanes, cold winters, hot summers — and even seagulls dropping the sharp remnants of their crab dinners — were causing the roofs to age prematurely.
Thanks to minor repairs made along the way, there were no leaks or other issues; however, the condominium association’s board of directors and property management company wondered if replacement time had come.
The maintenance team at REI Property Management asked several contractors to bid on a full replacement. In what proved to be the winning proposal, however, Advantage Roofing & Siding of Milford suggested something different — restoration with silicone coating.
The project shows the good things that happen when both contractors and customers focus on doing things the right way. The condo association’s board was proactive and acted before problems arose, and then kept an open mind in weighing its options. For its part, Advantage did its due diligence in recommending the best solution for its client and then cut no corners in delivering a high-quality project.
The Advantage team also learned and adapted along the way, finding new ways to ensure quality and boost crew efficiency – best practices they will use on future projects.
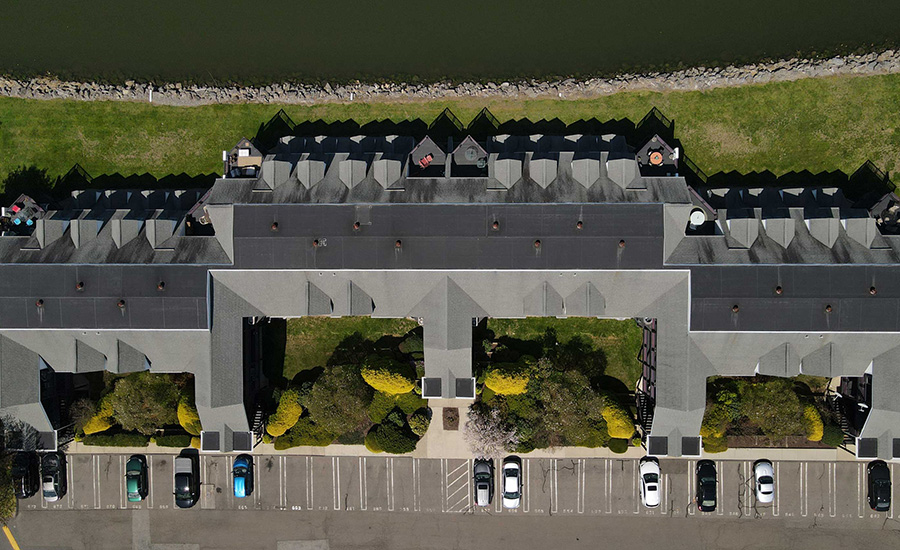
Coating the roofs of the condo complex would cost approximately 60% less than replacing them.
Pre-Project Homework
Before recommending coating, Advantage took the necessary steps to confirm the roofs were, in fact, good candidates.
Co-owner Mark Villano and Lead Foreman John Girardi inspected the roofs, looking for any soft spots where water had penetrated, any deteriorated edges, or any seams or details that needed attention. In a follow-up inspection, a technical representative from roofing system manufacturer Mule-Hide Products Co. walked the roof with them and discussed options.
Finally, core cuts provided a picture of the history and condition of the entire system, from the membrane to the roof deck. The roof remained sound with no underlying issues.
“These roofs were the best possible candidates for coating,” said Mule-Hide Products Territory Manager Tim McDermott.
An adhesion test confirmed that Mule-Hide 100% Silicone Roof Coating would be compatible with the substrate and that there was nothing, such as encapsulated moisture, that would inhibit adhesion.
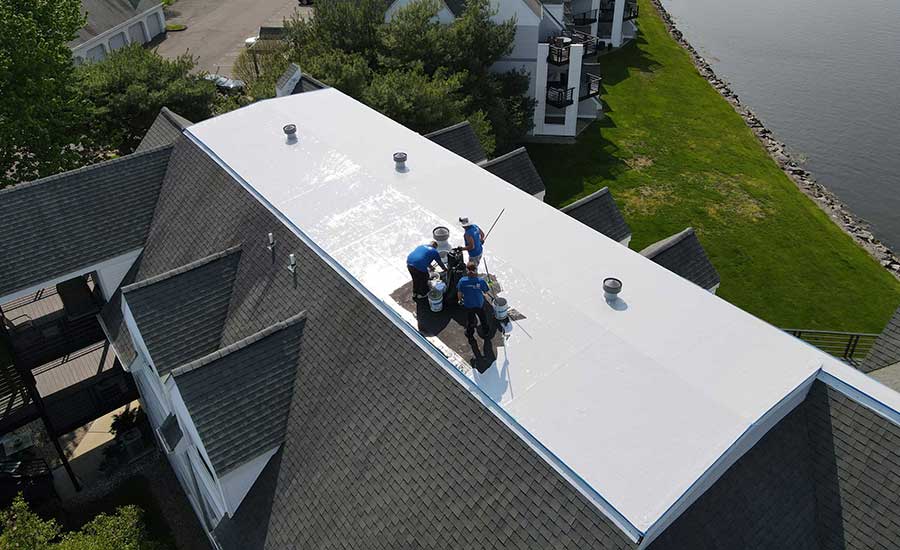
With approximately 315 squares of roof across seven buildings, it was the most significant coating job Advantage had undertaken.
A ‘No-Brainer’
Villano, Girardi and McDermott then met with the condo association’s board and made the case for restoring the roofs.
“It was almost a no-brainer,” said REI Property Management Maintenance Supervisor Charlie Scrivines.
Coating the roofs would cost approximately 60% less than replacing them. A 20-year, no-dollar-limit system warranty and a 50-year limited warranty on the materials would take the roofs off the board’s list of things to worry about.
There remains the potential to recoat the roofs in the future, further extending their lives. There would be minimal disruption to residents. The reflective coating would lower residents’ energy costs. Finally, there would be tax benefits.
The project would be considered “maintenance,” so the total cost could be written off as an expense in the year Advantage Roofing completed the job. Replacing a roof, on the other hand, is generally considered a capital improvement, and for tax purposes, the cost-benefit is a depreciation over 39 years. (Note: Property owners should consult their tax and accounting professionals for guidance on their specific project.)
With approximately 315 squares of roof across seven buildings, it was the most significant coating job Advantage had undertaken. They expected it to take an entire month, but smart logistical decisions, careful attention to detail, and a willingness to learn and adapt processes during the process allowed the 10-person crew to finish in just three weeks.
Easing Roof Access
One of the best choices Advantage made in planning the job (and one that was almost not made) was renting a 150-foot super boom man lift to access the roofs.
While the buildings are only three units high, the site’s quirky terrain creates a much greater distance between ground and roof. Using 50-foot ladders to access the roofs would have been “a nightmare,” Girardi said.
Advantage determined that using ladders would more than double the time required to complete the job, tire the crew, increase the risk of accidents and create the potential for coating to drip onto the buildings’ siding or shingled roof sections.
A Sunbelt Rentals representative toured the job site and took measurements before recommending the appropriate lift to cover the required distances and handle the weight of crew and materials.
“They gave us the perfect lift for this job,” Girardi said. “If it had been any smaller, we would have been in a bad spot.”
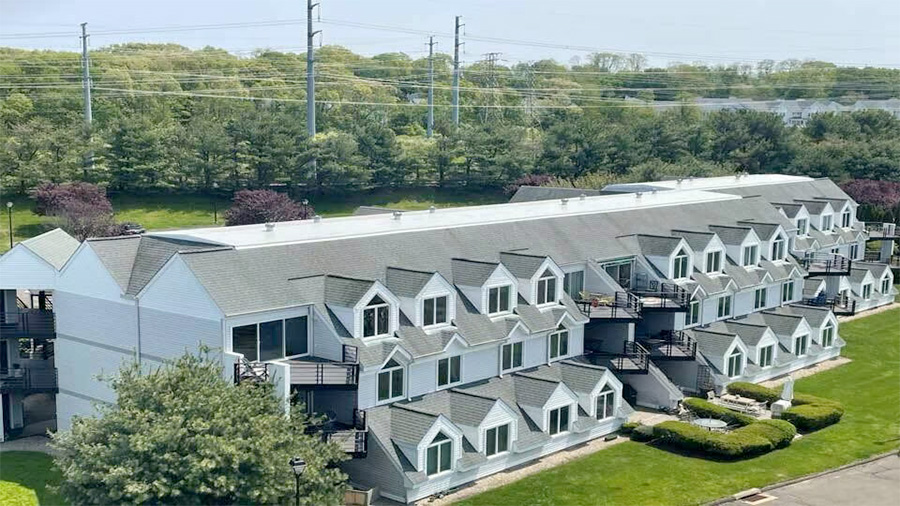
Location: Milford, Conn.
Roofing Contractor: Advantage Roofing & Siding, Milford, Conn.
Project Plan: Coat and restore an EPDM roof with a silicone coating after determining whether the substrate and membrane were sound.
Best Practice Learned: Added a 15-inch surface cleaner attachment to the pressure washer, which gently scrubbed the surface in a circular motion, cleaning it thoroughly without damaging it.
Highlights: Approximately 315 squares of roof across seven buildings. Rented a 150-foot super boom man lift to access the roofs, which became vital for safety and completing the project in three weeks. One coat of 100% Silicone Roof Coating from Mule-Hide Products Co. was applied at a rate of 2.5 gallons per square foot to reach the desired thickness of 40 wet mils/38 dry mils. A 20-year no-dollar-limit system warranty and a 50-year limited warranty on materials took the roofs off the condo association board’s list of worries. Considered “maintenance,” the total cost of the project could be written off as an expense in the year completed.
Squeaky-Clean Surfaces
For the coating to adhere correctly, removing years of accumulated dirt and EPDM dust was first required. While essential, the step can often be tedious and time-consuming. The Advantage crew took to the internet in search of a better way, and by the time they began work on the second roof, they had found it.
As before, they applied the 115 Cleaner from Mule-Hide Products and let it sit for the specified time. But rather than just using the spray from the pressure washer to remove the cleaner and dirt, they added a Ryobi 15-inch surface cleaner attachment. The inexpensive tool gently scrubbed the surface in a circular motion, cleaning it thoroughly without damaging it.
“We covered so much square footage so much faster,” Girardi said. “You’re really doing yourself a disservice if you’re not using something like this.”
Divide and Conquer
With seven roofs to tackle, the crew split into teams, ensuring a continuous workflow. While one team was coating one roof, another was preparing the next one, cleaning the membrane and applying Seal-Fast Liqui-Flash from Mule-Hide Products to seal edges and details. Crew members also would backtrack to do quality checks and complete any necessary touch-ups.
Meticulous Attention to Detail
To reach the desired thickness of 40 wet mils/38 dry mils, a single coat of 100% silicone roof coating was applied at a rate of 2.5 gallons per square foot.
Because of the windy coastal conditions, application with a sprayer was not an option and instead, crews used rollers.
Some easy math and chalk lines helped ensure that the coating was applied at the correct thickness. The crew calculated that one pail of finish coating would cover 200 square feet of roof surface. By marking off 200-square-foot sections, they could simply empty the pail in the middle of a square and spread it, confident it was the desired thickness.
To ensure even application, the crew pushed the coating into place rather than rolling it back and forth as when applying paint to a wall.
“Sometimes the roller isn’t even moving much because you don’t want to make it too thin,” Girardi said. “You can visually tell that the coating is even.”
A Success for All Involved
The proactive approach, careful planning and meticulous work paid off.
“It was a really good experience for us,” Girardi said. “Even the field tech who did the warranty inspection was amazed at how it transformed the rubber roof to what it looks like now.”
Scrivines, REI’s property manager, concurred, saying how the job went as smoothly as a job could and paid compliment to the crews’ communication efforts.
“They were right on point with everything in terms of delivery times and getting the job done on time; everybody was very happy with the work from beginning to end,” he said, adding, “If we had waited another two years, we probably would have needed to replace two of the roofs; now we’ll be good for another 20 years.”
Report Abusive Comment