The advantages of powder coating are numerous for aluminum building products. Powder coating offers an excellent finish, strong performance, and customization while providing a more environmentally sustainable and cost-effective solution for long-term durability.
These advantages are crucial to the architectural industry since environmental concerns and building construction and maintenance costs are ever-increasing. All building aluminum architectural elements such as window or doorframes, storefronts, curtain wall structures, façade panels, roof edges, column covers and other decorative components are enhanced with a powder coating finish.
Powder coating has been popular in European architecture since the 1970s when environmental issues began moving to the forefront in the design and construction space. Increasingly over the past two decades, design and construction professionals in the U.S. and other parts of the world have begun to embrace powder coating for the built environment.
This is due mainly to coating technology improvements, making powder coating of aluminum superior to wet paint finishing in most applications, as well as the drive for greater sustainability and cost containment in manufacturing processes.
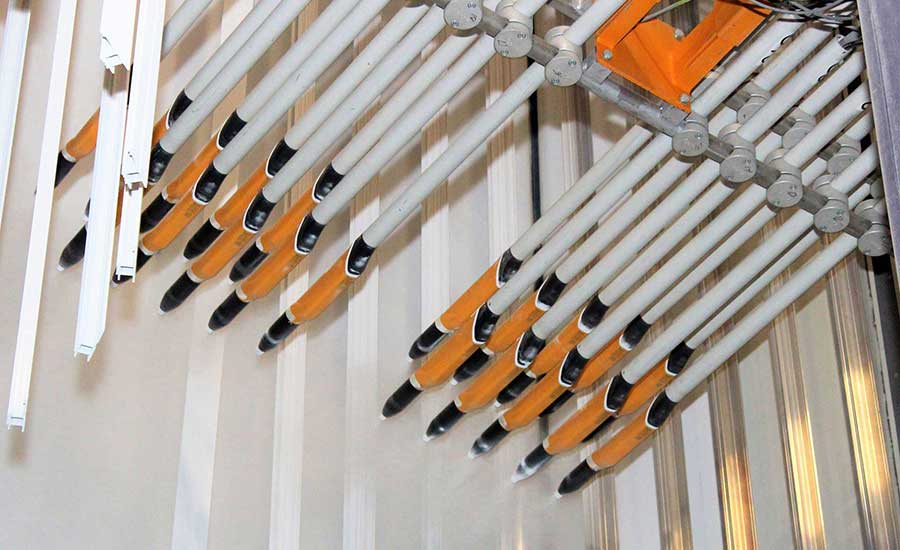
National manufacturer Crystal Window & Door Systems has vertically integrated its production operations with aluminum extrusion and finishing, offering greater quality and cost control, shorter lead times, and a wide variety of powder coat finishing options for aluminum building products.
Market Growth
With enhanced awareness of its benefits, powder coating for aluminum architectural products has enjoyed substantial growth in recent years. As cities and states nationwide enact more aggressive environmental codes and architects specify products with greater sustainability in building design, building product manufacturers are evaluating the cradle-to-grave implications of their products.
For aluminum product finishing processes, powder coating offers substantial environmental benefits, including:
Low Volatile Organic Compounds (VOCs) and no toxic compounds in powder coatings
Single coat factory application and no jobsite application required
Powder overspray reclamation and reuse
Non-chrome pretreatment of aluminum
Superior scratch, weather, and corrosion resistance for long-term durability
Superior color and gloss retention
Lower temperature curing with lower energy costs
No hazardous production waste
EPA recommended
LEED point contribution
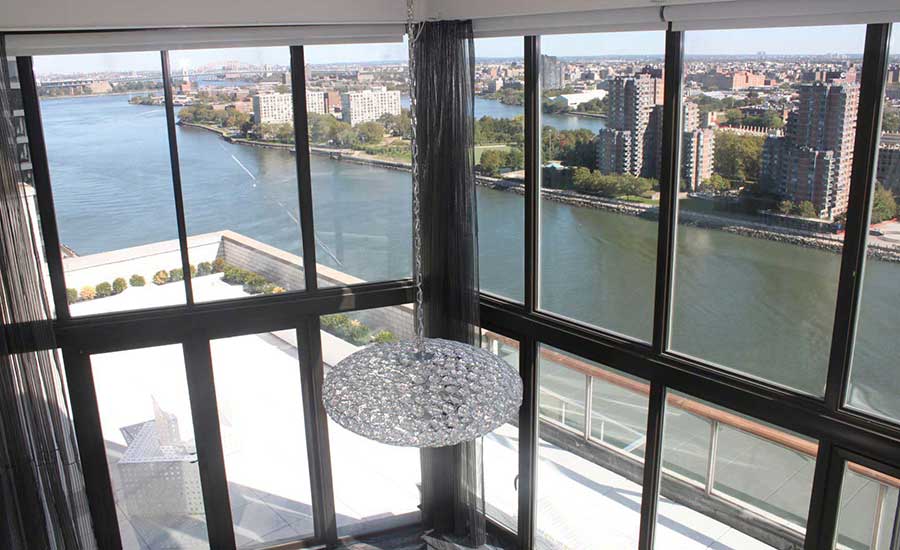
Shown here is just one example of the projects Crystal Window's products can create using a variety of custom and standard colors.
From Paint to Powder
In 2003, Crystal Window & Door Systems purchased an existing aluminum fabrication facility in Union, Mo., to vertically integrate operations and control quality and cost for its growing aluminum window product lines. Crystal’s subsidiary Gateway Extrusions today offers extrusion, fabrication, and finishing services for a wide range of aluminum products.
Initially, Gateway’s aluminum extrusions were finished with liquid paint, as was typical of the industry. However, soon after starting operations, the company opted to replace the paint line with a new, more modern powder coat system.
Gateway’s powder coat line enables the company to accommodate the demand for more consistent finish quality, longer profiles, and faster turnaround in the architectural market.
Powder coating equipment comes in horizontal and vertical configurations, each with benefits. Horizontal powder coat systems permit even coating of large flat components, such as shutters and panels, or smaller components, such as fence caps and light fixtures, regardless of orientation on the line.
They are ideal for finishing companies handling smaller batch jobs, shorter lengths of aluminum extrusions, and frequent color changes. They are also well suited for production facilities with limited ceiling height, without the same level of capital investment required for vertical powder coat systems.
Vertical powder coating lines offer faster production speeds, can handle longer components, and require less floor space for pre-treatment, powder application, and drying than horizontal lines. They do require significantly greater ceiling heights, however. Gateway had to build an addition with a 50-foot ceiling height to accommodate its new vertical line. Vertical lines are most cost-effective for finishers with high volume, large batch jobs.
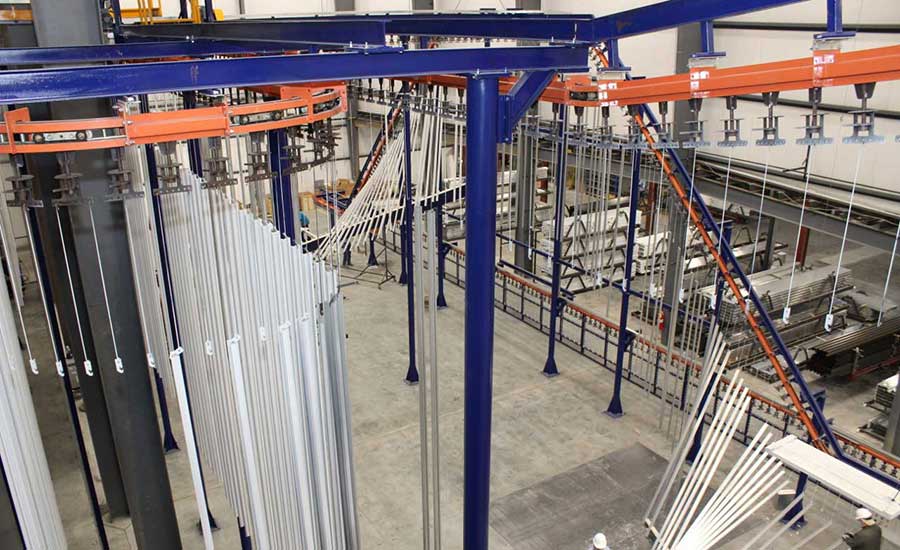
Seen here is Crystal Window's subsidiary Gateway Extrusions’ vertical powder coating line in Union, Mo.
Supplier Partnerships
Building strong relationships with powder suppliers and application equipment manufacturers is critical for powder coating finishers. Several challenges to the supply chain within the powder coating industry demonstrate how important these relationships are.
Over the past two years, raw material shortages and cost inflation have raised costs for powder components such as resins, curing agents, and pigments and forced many powder suppliers to put customers on allocation. This has caused greater lead times for product finishers providing a wide range of aluminum building products and increased costs and surcharges.
Products such as solar panels used to power smaller products, medical devices, electronic equipment, and Lithium-ion batteries for electric vehicles also use resin, which puts tremendous strain on resin component availability.
The Future of Powder Coating
Façade product powder coating will continue to grow due to its superior performance and “green” characteristics. Architects are increasingly aware that powder coating can perform well in even the most severe climates — harsh sun, salt air and spray, and temperature extremes — and will continue specifying powder coating to protect aluminum windows and other façade elements.
Building product manufacturers will seek powder-coating fabricators certified for AAMA durability performance standards 2603, 2604, and 2605 to meet this demand. They will also promote powder-coated products as the more sustainable choice, helping construction and renovation projects earn LEED points and meet sustainability goals across the country.
The future for architectural product powder coating is bright.
Report Abusive Comment