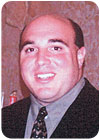
Proper application of sprayed polyurethane foam (SPF) systems is required for the long-term success of the system. Installation is comprised of three stages:
- Substrate preparation.
- SPF application.
- Coating application.
Each phase has its own idiosyncrasies that require proper attention. The materials should be applied by skilled applicators in accordance with the material manufacturer's requirements.
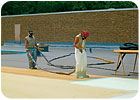
Photo courtesy of Arkema Inc.
Substrate Preparation
SPF systems involve adhered materials that require clean substrates for proper adhesion. The substrate - whether it is for new or recover applications - should be free of all dirt, dust and contaminants that can have an adverse effect on the adhesion of the foam to the substrate. Removal of dust and contaminants can be completed through the use of air pressure, vacuum equipment, manual brooming or sandblasting, depending on the substrate surface and the severity of the contaminants.Surface moisture can also have a detrimental impact on the foam's adhesion capacity. SPF is typically comprised of a mixture of two components: isocyanate and polyol. Moisture that comes in contact with the foam during application can disrupt the mix ratio balance of the two components, creating foam with a soft, spongy cell structure. The foam in this state is weaker, less thermally efficient and susceptible to blister formation. On new construction projects, moisture on the surface is easily detectable. Moisture in the existing system on recover applications must be determined through a proper moisture analysis. All wet materials should be removed prior to the SPF application.
Application of SPF over existing roof systems requires further preparation procedures. In addition to removal of all wet materials, all defective membrane conditions (blisters, ridges, splits, etc.) should be cut out and properly repaired. Anchoring of poorly adhered membrane or insulation is required. The existing system should also be free of all irregularities that would impede proper SPF adhesion, such as voids or mastics. All flashing materials should be properly repaired of defects and securely anchored to the substrate. The SPF applicator should also ensure that all penetrations are properly waterproofed prior to the application. All drains and penetrations should be masked. Piping, electrical conduits and electrical lines should be relocated prior to SPF application, as they should not be covered in the SPF application process.
SPF Application
The foam spraying operation is the most critical point of the SPF application. Application rates and weather conditions must conform with the manufacturer's requirements. Application of SPF is completed in lifts (the foam thickness sprayed per pass), since the foam is not applied to its total thickness in one spray application. Typical SPF applications require a minimum total thickness of 1 inch with a minimum of 1/2 inch per pass. Once the foam is sprayed in place a base coat is required to protect the foam from ultraviolet radiation. The total foam spray thickness and base coat application must be applied the same day, and larger roof areas should be segmented into sections to achieve full application on a daily basis. Cure time is based on ambient temperatures and the thickness of the foam application. The manufacturer should be consulted regarding the proper cure time, and all roof traffic should be avoided until the SPF is completely cured.The surface finish must be applied in a smooth, even application. The surface should resemble an orange peel (or a coarse orange peel). Surfaces that resemble popcorn will require additional coating because these finishes are susceptible to cracking and openings. The surface finish must be completed with the SPF manufacturer's approved coating at approved application rates. SPF application should only be completed by properly trained and skilled applicators.
Ambient weather conditions can also contribute to the success or failure of these systems. SPF is a temperature-sensitive material and there are strict temperature regulations (as there are with other roof systems). Application must not be completed in wet conditions or if there is a call for precipitation prior to proper cure. The ambient outside temperatures during application should be above 40°F or within 5° of the dew-point temperature. Because this is a sprayed application, wind speeds should be below 12 mph on projects without windscreens (such as parapet walls, etc.) and 20 to 25 mph when there are windscreens.
Report Abusive Comment