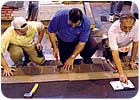
Over the course of the year, your company probably spends a significant amount of time and resources in providing training in such areas as computer operations, equipment operation and organizational procedures. These are all important elements of a successful company. However, they are all ancillary items, which can increase efficiency but do not add to the bottom line. In most cases, the type of formal training that will benefit your company the most is never provided: training for the applicators.
In the past, the roofing trade was a skill that was passed down from generation to generation within families. Fathers and uncles often served as mentors to those in succeeding generations. Most mechanics started roofing in their teens and stayed in the profession through retirement. Hands-on training was conducted at the jobsite in the midst of the daily production run. If aspiring mechanics failed to grasp a skill and it hampered the day's production, they were ridiculed to the point of never making the same mistake again.
At one time, this type of training was effective. There was a consistency in the work force and a limited number of roof systems to learn. Today, there are a plethora of roof materials and systems, each with their own idiosyncrasies depending on the manufacturers requirements. The labor force has become more diverse and there are fewer multigenerational mechanics and more inexperienced applicators. Information gathered from discussions with roofing contractors throughout the country indicates that there is a labor shortage in this industry. In this respect, the roofing industry is similar to most other construction trades, which are not attracting younger workers in numbers that they had in previous decades.
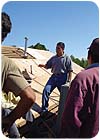
Photo courtesy of CARE®.
The Proper Training Program
There are a number of advantages to a worker training program. Properly trained workers become more proficient at their jobs and elevate their production rates sooner than un-trained workers in the same positions. The quality of their work also increases as they eliminate repetitive mistakes that - in the case of roofing - lead to callbacks for leak repairs. Studies indicate that individuals that have a comfort level in their work skills will remain in their jobs for longer periods. This could eliminate high employee turnover levels.The most important aspect of a training program is that it must be provided to all applicators. Offering training to only foremen or superintendents and relying on them to effectively communicate the training methods to applicators could eliminate the transmission of critical information. Not all supervisors are effective communicators.
The roof is one of the only major building components that is fully constructed on-site. It is a system of components and diverse materials. Although there is some repetition in component applications, detail work can vary from day to day. Specialty crews that apply the same types of systems on every project are becoming increasingly rare. The current roof mechanics are being asked to apply all types of systems and may not complete the same system on two consecutive projects for months. This requires applicators with greater versatility. Because of this fact, training for all types of systems is required.
Unions provide training for their members. To achieve journeyman status, mechanics are required to complete a scheduled training program coupled with on-site experience. A distinct advantage to union membership is that employers have a pool of trained mechanics available for employment. Non-union contractors can build a skilled work by providing their own training.
The best way to establish a training program is to make it a mandatory condition of employment. Most retail chains and restaurants provide a required training program prior to employment. These programs are even required for part-time employees. The frequency of the training program depends on the turnover rate of your employees. If you are fortunate enough to have a stable work force, training may only be required on an annual basis. Companies with higher turnover ratios will require more training sessions.
The training can take place at your company's headquarters or through an outside source such as at manufacturers facility. Some building owners may also let you utilize their roof for training procedures, particularly if you provide the work at a discounted rate. These are good scenarios because they mirror real world conditions. However, if you have to provide price breaks, they could become costly.
Sources of Help
Manufacturers can also prove to be an excellent source of training. In fact, a requirement of becoming a certified applicator for most manufacturers is through completion of a training program. Contractors and manufacturers would benefit of the actual work crews enrolled in these training sessions, instead of regulating it to a "paid vacation" of supervisors and project managers. To avoid costs associated with sending your entire crew to these sessions, arrangements should be made to have the manufacturers provide in-house training to your company. Most manufacturers would readily dispatch a representative to provide this valuable training on proper system application methods. In the long run it will be of benefit to them as well.The National Roofing Contractors Association (NRCA) offers a wide variety of roof application training materials. Training materials are provided on all types of roof systems, safety procedures and application methods. The training materials can be purchased on DVD, video or manuals. Contact the NRCA (www.nrca.net) for more information about the proper training tools for your company. Another excellent resource is the Center for the Advancement of Roofing Excellence (CARE®), a not-for-profit organization founded by GAF Materials Corp. that holds training sessions at various forums at a variety of sites, including plants, distributors, association meetings and conventions.
Proper training should include hands-on application procedures for each roof component. Every individual should conduct each application method. Education studies have indicated that information is best obtained through repetition. It is also important that definitions for why things are done are almost as important as explaining how things are done. This is a critical element in training and should be stressed so that each individual can process the information properly.
The training sessions should be open to all employees, not just recent hires. The experienced mechanics should attend the training to sharpen their skills and to learn new application methods, materials and detail installation procedures. The industry is currently progressing at a rapid pace and there is a continual influx of new materials and application methods.
To meet the future requirements, contractors must employ skilled applicators that are proficient in current system requirements. Proper application training should increase productivity and effectiveness of the crews, increasing the company's bottom line. The training will also increase the employee's comfort level and, in turn, decrease employee turnover rates.
Report Abusive Comment