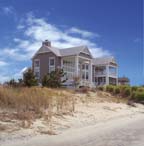
Traditional Terne
Terne coating has been, for both performance and aesthetic reasons, the most popular and predominate alloy in roofing materials for many years. Terne features low cost, ease of application, excellent corrosion resistance and, the formation of a soft and elegant patina over time. The traditional terne coating, however, contained nearly 80 percent lead. Terne manufacturers took a responsible and proactive approach to identify new materials that would provide all of, or greater benefits, without posing any environmental concerns. A respect for environmental issues has brought with it enhanced product features that provide not only a safe product, but better roofing products overall."Lead can no longer be used in solder or paint, but it can still be used elsewhere only so long as it doesn't get into the air, soil or water," explains Dr. Mehrooz Zamanzadeh, NACE (National Association of Corrosion Engineers)-Certified corrosion, coatings, materials selection, and design specialist. "The Clean Water and Clean Air Acts provide federal limits on lead concentrations in water and air, and each state's EPA has its own set of regulations on soil lead concentrations. Permissible concentrations of lead in human blood have been steadily decreasing for the past 50 years, perhaps as a result. It's a useful element that remains in the marketplace, but it is certainly very toxic-so any effective substitute is welcomed."
In addition to the lead-based alloy hazards, an unforeseen phenomenon in the early 1990s was indicated by widespread reports of the formation of unappealing red discoloration on lead-bearing coatings in roofing applications. With the help of Dr. Zamanzadeh, Follansbee conducted an investigation and discovered that the formation of the unsightly discoloration was due to the reduction of sulfur in the atmosphere, probably as the result of EPA legislation mandating the reduction of sulfurous compounds from flue gas emissions.
The red stain was the knock-out punch for lead, and strongly suggested the need for a new alloy to meet the needs of the roofing industry. The new alloy would need to protect roofs from corrosion at least as successfully as lead, maintain environmentally responsible standards, and produce an aesthetically acceptable patina with no splotchy discoloration. Because aesthetics were important, the spangled look of hot-dipped zinc would be unacceptable. No one had yet been able to produce an alloy to these specifications, though many had tried.
Zinc/Tin Development
Follansbee doggedly pursued the perfect alloy. Very much like latter-day alchemists the company labored to find the elusive combination that would, in a manner of speaking, turn lead into gold. After years of metallurgical research and testing, Follansbee secured a patent on ZT® alloy, a proprietary combination of zinc and tin. And with no lead.
"Follansbee was determined to create a material that was free of lead, corrosion resistant and environmentally friendly," notes Zamanzadeh. "These goals were pursued with extensive laboratory testing and laboratory test-trials."
The high zinc content (50 percent) of the alloy had never been used on architectural materials. But metal building and roofing manufacturers immediately perceived the advantages of zinc alloy substrates and began developing their own coatings to enhance their product lines.
In retrospect, environmentally friendly zinc/tin alloys are, in fact, proving to be far superior to lead-based alloys.
Benefits
The principal advantage of zinc/tin alloy roofing is its excellent corrosion resistance in marine and industrial environments where other roofing metals quickly corrode. A coating created by adding zinc to tin, which is then applied to either stainless or low carbon steel materials, exhibits corrosion-resistant properties exceeding those of tin-only and traditional terne roofing.The zinc/tin coating is not limited only to protection of stainless and carbon steel, but may also be applied to other metals such as copper, bronze, tin and titanium.
ZT alloy is oxygen-reactive and forms an attractive gray surface patina, but prevents corrosion from the presence of carbon dioxide, chlorides, or other reducing agents in the environment, significantly extending the life of the material. As a result, zinc/tin alloys inhibit corrosion of exposed metal anywhere in the vicinity of the coating. This is a crucial advantage, assuring that minor discontinuities in the coating-either resulting from the coating process itself or created during fabrication or installation-will not fail to protect the substrate from rust. Remarkably, even the patina covering the zinc/tin protective layer is itself an inert corrosion barrier, shielding the alloy and further enhancing the overall protection of the steel substrate.
Coatings of metallic zinc are generally regarded as the most economical means of protecting against corrosion. Seven methods of applying a zinc coating to iron and steel are in general use: hot dip galvanizing, continuous-line galvanizing, electro-galvanizing, zinc plating, mechanical plating, zinc spraying, and painting with zinc-bearing paints.
Testing
The behavior of zinc and zinc coatings during atmospheric exposure has been closely examined in tests conducted throughout the world. Precise comparison of corrosion behavior in atmospheres is complex because of the many variables involved, such as prevailing wind direction, the amount of sea spray, and the relative periods of moisture or condensation and dryness."Steel roofing materials are tested for corrosion-resistance in a salt spray cabinet per ASTM B117, a condensation/atmospheric chamber per ASTM D4585, and also for electrochemical testing," adds Zamanzadeh. "Most roofing materials exceed 2,000 hours before the material begins to develop red rust. But Follansbee materials surpassed 5,164 hours with zero sign of red rust."
In addition to its performance in corrosion resistance, Follansbee's roofing materials showed no uplift blistering or loss of adhesion. Testing results prove the effectiveness of the ZT alloy and solidify its position as a successful replacement for lead.
Formability, Solderability and Durability
Yesterday's lead coatings and today's alternatives serve several functions, in addition to corrosion resistance. Formability, solderability and durability are also critical roof characteristics.The ZT alloy's dull surface has excellent low temperature properties, exceptional solderability and formability, and provides ease of installation in any weather condition.
Zinc/tin-coated stainless steels have about the same tensile and yield strength as mild steel but a much higher ductility. The higher strength of zinc/tin-coated stainless steel means that higher loads of forces are required to bend the material. However, stainless is generally used at a much thinner gage, enabling it to be formed easily with conventional roofing tools. The flexibility and formability is critical to installation. The zinc/tin coating offers dual benefits of strength and formability.
As the demands and regulations of the environment and the needs of architects and contractors continuously evolve, the metal roofing industry, and all building products, must also evolve. Ongoing testing and research of both new and long-existing materials are essential to developing the best and safest products. The outstanding performance of the top products available today clearly demonstrates the commitment to excellence of the leaders of the metal roofing industry.
Metal roofs are a great example of a man-made building product that has been used for centuries. Thanks to research and testing, metal remains a highly functional, aesthetic, and now technologically advanced roofing option.
Report Abusive Comment