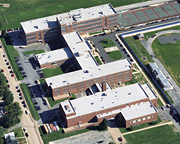
Roof coatings are complicated systems that need to be well understood to maximize their benefits. The aforementioned bulk materials haven’t changed significantly in recent years; however, the technology of roof coatings continues to advance as scores of companies research new formulations for new applications. Roofing contractors need to keep up with these developments as part of their continuing education.
New Hats for Roofers
Besides being accomplished as a traditional roofer, a roofing contractor today needs to be part chemist, part ecologist, part maintenance engineer, and part master coating applicator. Roofing contractors also need to be good educators, because building owners generally don’t understand roof coatings very well. They rely on contractors to select coatings and methods of application; yet, roofing contractors often need to explain the rationale for their choices. While roof coatings are based more on science than art, building owners often lack a basic understanding of what they are, what they do and what they cost to own. Also, they often need to be educated on the need for an ongoing roof maintenance program.
Roofing contractors understand that the roof is one element in an “ecological” system that includes the building, the neighboring community and the even the global environment. They understand that energy efficiency and sustainable development are more than academic buzzwords.
Yesterday and Today
Most commercial roofers understand how to apply built-up roofing systems, which are based on conventional materials, such as asphalt pitch and coal tar. They also understand how to apply flashings, using various mastics that are available to them.However, roofing today is becoming more complex. The increased use of modified bituminous membranes has ushered in a new generation of cold-applied adhesives and cements for ensuring strong, durable, watertight bonds between the selvedges and end laps of the mod bit membranes, and for adhering the membranes to the roof deck. Many of these cold-applied systems have greatly reduced the installation times for roofing systems and reduced the risk of fire from open flames on the rooftop.
Roofers are also savvier about the vulnerable areas of a roof. Reputable contractors will take extra steps to ensure that these areas receive added protection, whether they are installing a residential or commercial roofing system.
Through all this change, one thing is certain. There is a growing recognition that roof coatings affect the performance of roofing systems and hence are critical components. Contractors are becoming more knowledgeable of the coating options for various roofing systems, and they are becoming more likely to offer various coatings to building owners as part of either the initial installation or an ongoing maintenance program.
The Protective Layer
Ultraviolet radiation and visible light from the sun repeatedly impinge upon the outermost surface layers of roofing systems, accelerating oxidation and chemically degrading the roof system, causing it to become brittle. And if these challenges weren’t enough, water in the form of rain, snow, sleet and hail further compounds the destruction through erosion, expansion and contraction forces, and mechanical impact.The application of a roof coating on top of a conventional roofing system can act as the final shield against these forces of nature. This protective coating can increase the expected life cycle of a roof and also improve the energy efficiency of a building.
It can resist baking by the radiation from the sun and the chemical attack. It can prevent the formation of microcracks that otherwise would collect dirt and chemicals and grow into larger cracks.
The optical properties of a protective coating also determine how well the roof reflects sunlight back into the sky. Reflection of sunlight has an immediate effect of lowering roof temperatures. Since chemical reactions often increase exponentially with temperature, a roof with a good reflective coating is not going to deteriorate as quickly as one that has no coating and hence is exposed to higher temperatures on a daily basis.
The underlying roof may provide excellent moisture resistance in the event of rain, but a coating often is essential to protect this waterproofing agent against other forms of erosion and degradation.
Roof Maintenance
Despite the fact that the cost of maintaining a roof can account for as much as 90 percent of the total building maintenance cost, most building owners have a tendency to overlook this critical building component and the importance of a regular roof maintenance program until it may be too late. By this time, the roof system either has developed leaks or it requires extensive repair or replacement.Once a roofing system is installed, many building owners and managers hold an “out of sight, out of mind” philosophy. They generally do not consider the variety of chemical and physical stresses that roofing systems are exposed to regularly. Airborne particulates, chemicals and debris collect on the roof, clogging drains and damaging the roof and its components.
But a properly planned and executed maintenance program, including the use of roof coatings, can prolong a roof’s life and substantially reduce the chance of serious leaks. The cost of proper maintenance generally is much less than the damage and repair costs that can be avoided, and it is less than the intangible but real disruption costs of a reroofing project. Consequently, routine maintenance can reduce the total life-cycle costs for the organization.
Many Types, Three Categories
Many coatings are intended for use on specific roof types and sometimes their application is limited to specific climates. Generally speaking, when it comes to coatings one size does not fit all. Proven coatings exist for most low-slope roof systems, such as built up, single ply, modified bitumen, metal and SPF; and for a number of steep-slope systems, such as metal, ceramic tile and SPF.
Some coatings are an integral part of the original or reroof system, while others are designed to maintain particular systems, either as a part of the manufacturer’s system warranty program or as part of the owner’s maintenance program. Roofing contractors should be aware of the variety of roof system types, the specific requirements that are associated with each system, the type of coatings available, and the benefits they provide. Essentially, roof coatings can be grouped into three categories: functional coatings, reflective coatings and maintenance systems.
Functional Coatings
Functional coatings are generally low-technology materials that are chemically compatible with the primary roof membrane. They protect the roof membrane by preventing direct exposure to solar radiation, atmospheric elements and water. They also can seal minor imperfections in the membrane. Classic examples include fibered solvent-based asphalt and coal-tar coatings and bituminous emulsions.
If the underlying membrane is in good condition, a maintenance program that includes periodic application of this sacrificial type of coating can cost effectively extend the life of a conventional roof by one to three years or more.
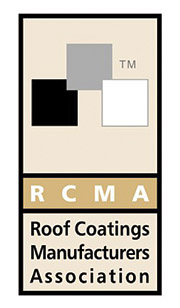
Reflective Coatings
Reflective coatings protect and extend the life of the roof system by reflecting a substantial portion of the solar radiation that reaches the roof surface. By shedding this energy before it is absorbed as heat, the reflective coating can substantially reduce both the peak temperature and the daily temperature cycle seen by the roof membrane. Depending on a number of factors, including the geographical climate and building design, reflective coatings also can result in reduced building energy costs.Most reflective coatings use either aluminum metal or white titanium dioxide pigments to reflect or scatter sunlight. They tend to be moderate- to high-tech materials, and they come in a variety of technologies and grades. Reflective coatings, especially water-based coatings, tend to be much more sensitive to the exact type of roof membrane to which they are applied, to the cleanliness and preparation of the roof surface, and to weather conditions while the coating cures.
Even modest reductions in the peak temperature and the temperature cycle of the roof will significantly extend the life of the roof. This benefit is particularly true for well-insulated roof systems, which tend to run hotter because they cannot shed heat into the building. Well-insulated black roofs generally have a shorter life than the identical system that is placed over a roof with less insulation.
It is important to select the coating to be compatible with the roof, and the roofing contractor must follow the manufacturer’s preparation and application instructions exactly. Following these guidelines, a performance life of three to seven years can be expected, depending on factors that include climate and slope.
Report Abusive Comment