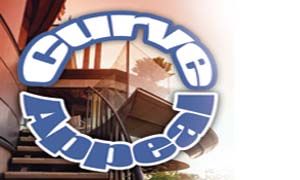
The rapid growth of metal roofing is expanding into new markets as more and more architects, designers and building owners become used to the concept and price. Many credit the mainstreaming of metal roofing to an increase in demand for curved, or radius, metal panels. From accenting an entrance or softening the harsh lines of a big box store, the appeal for a permanent architecture feature is worth the investment. For many building owners and the architects they hire, the unique designs are simply an attractive alternative to the fabric-covered mansards that adorn commercial buildings yet don't have the longevity.
"These people are starting to put in curved panels because it's functional and, for the long term, it's cost effective for them," says Sid Glasgow, owner of Glasgow Roofing in Charleston, S.C. "If you can put it in, it's a little twist for them."
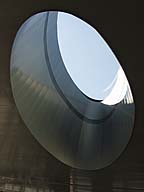
A New Twist
While hard numbers on metal roofing are difficult to quantify - other trades like sheet metal contractors and metal building producers install their fair share of metal roofing - there are many indications that curved metal panels are experiencing their own boom. Roofing Contractor's Metal Editorial Survey in 2001 showed that the 5 percent of roofing contractors surveyed who were planning to purchase a curved panel roll forming machine in the next 12 months have made good on their promise, and then some. Geoff Stone, president of MetalForming Inc., Peachtree City, Ga., says that he's sold 260 curving machines in the past three years and there's no let up in growth.In the RC survey, 50 percent of the respondents said they always used factory-formed panels and 63 percent had never roll formed panels with their own machinery. However, there is a definite trend towards bringing the sophisticated process in-house, saving time and reducing costs associated with shipping, waste and change orders. The increased automation of brakes and formers has created a cottage industry of local manufacturers, some of which curve panels for the big boys.
"In our area we're starting to see more of (curved metal panels)," says Dennis Johnson, owner of Bridges Steel Inc., Belgrade, Mont., a sheet metal fabricator. He purchased his first curving machine last year from MetalForming. "We can see it coming. It's been fun. It's been pretty lucrative for us too." He adds, "We started to get a lot of interest from contractors and inquiries from architects. I just figured it was probably time to get into it. If you buy it, they will come."
The former cattle rancher got tired of that volatile market, so after seeing how well friends in Ontario - where he grew up - were doing with sheet metal fabrication, he set up his shop in 1996. The company does not do any installation and sells only retail to roofing contractors and individual homeowners. It seems that the rugged individualism that thrives in Montana takes on many forms as Johnson goes over roof installation basics and rents out standing seam machines. From pole barns to custom homes, his customer universe is usually within 150 miles and he estimates that at least one third of his sales are directly to consumers.
"People around here are not afraid to conquer stuff," he observes, adding that if there are too many cuts in the roofline, he'll recommend they try another material. "I like to sell metal, but I also like to have somebody happy down the road. Snow can really wreak havoc on metal roofing. There are some situations it just won't work in."
For radius panels, he sells floating clips to handle the expansion and contraction of the seams. He also highly recommends applying a mastic in the seams for those "Chinook" days when the sun melts the snow and can penetrate mechanically seamed panels that aren't waterproof. He prefers the standing seams to battens, which have a risk of being pulled off by falling snowdrifts or thermal expansion.
Johnson is driving his own sales with a 1,200-square-foot office that displays the various panels his company fabricates. Using interior soffits, ceilings, counters and wainscot, customers (professional roofing contractors, commercial building owners and homeowners) can see and touch the actual product. Last year, the company opened a 4,000-square-foot satellite office and shop in Billings - about 120 miles to the east - and he's already adding an additional 8,000 square feet.
Although Johnson maintains an extensive Web site, he claims that there's nothing like seeing the product in person. "You can tell people all day long, but when they come down here, we have samples they can feel and take home," he says. "It really makes up their mind about what they want."
Johnson prides himself in local service, dealing with customers individually, providing quick turnaround and saving costs in shipping, which is a big deal for many of the rural job sites. Some of the lengths of the curved panels he's producing are too expensive to ship, even for the high-end homes cropping up all over. Now that the economy is picking up, he's seeing a spike in business, particularly with curved metal panels.
"It's starting to take off. It's diversified my company," says Johnson. "We get the product out the door quick. We do a lot of custom stuff. The sky's the limit. If they can draw it, we can do it."
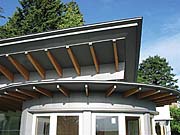
Growth Curve
Roll Former Corp. in Philadelphia has been making portable roll formers for over 25 years. Its first entry into curved metal panels was a custom machine for a company in 1987. According to John Dumke, director of sales and marketing, it's now a standard piece of equipment for the company, which derives about 60 percent of its sales from custom work. "The curved panels and curved tapered panels are a specialized field for roofing contractors," he explains. Although the process has become much more automated, "Not every contractor can or wants to do it."From S-curves to U-panels, Dumke admits that he doesn't always know what the job calls for when a machine goes out, but versatility is a big selling point. The U-panel formers can perform concave or convex panels from 10 to 24 inches in width. The S-panels have a snap-on cap system for standing seams and can also do false battens with a crinkle appearance. The company is developing a curving machine with a tapering ability used for domes.
"The tapered panels are becoming more and more popular than a straight run," Dumke says, adding that the quality of paint finishes is driving sales at the cost of less durable items like fabric mansards and domes. "I would think that a lot of that is due to the paint finishes. It's probably the longevity of it aside from the aesthetic appeal."
Although he doesn't think that the seams for curves have to be watertight due to their high slope, he's seeing a lot of contractors curving traditional standing seam panels then double locking them. Roll Former also strongly recommends a hot metal caulk for extra protection since callbacks on a dome or curve can be very costly. The company also offers a cap machine strictly for curved panels but does not require its customer to purchase them.
"We don't hold any of our customers hostage," he says. "What we do is help them out with the curve and make them a special set of cap curving rules if they buy them elsewhere."
The growth of curved metal panels seems to mirror or even surpass the growth of metal roofing in general. Market share for all metal roofing has increased over the years, from 5 percent of new commercial construction in 1994 to 25.5 of new "steep-slope roofing sales" in 2002, according to figures from the National Roofing Contractors Association annual surveys (strict comparisons are unavailable due to changes in methodology and breakdowns).
Glasgow, of Glasgow Roofing, founded in 1987, experienced so much demand for metal roofing that he started Charleston Metal Works five years ago to fabricate metal roofing for his company and others. He bought his first curving machine around the same time, along with a new radius seamer that seams curves and domes, and has never looked back.
"The majority of our business is curved panels and the associated curved trim," says Glasgow, who also fabricates curved panels for major metal fabricators. "It's a lot cleaner and a lot faster. Of course, the price comes down even further on that.
"It's definitely the architects driving it," he adds. "A lot of your school districts and hospitals that are looking for an improvement are using canopies on entries and wings."
It seems that as architects and building owners are trying to make their buildings more distinctive from the square boxes of the surrounding landscape, a curved canopy or mansard makes a world of difference. Even chains known for their frugality are trying new things, encouraged even further by metal's longevity.
As for the more traditional applications of curves, the capabilities of the new machines are constantly being pushed to the limit. When Glasgow Roofing reroofed the South Carolina State House, the company seamed much of the copper dome the old fashioned way with mallets, benders and brute strength. He then discovered a new process developed by a roofing contractor in Bavaria, Germany, that seamed radius metal panels while carefully preserving the finish. Using new tools in conjunction with CAD software that ensured precision cutting, Glasgow was so impressed that he bought the U.S. patent rights. "It's quicker, more efficient and every bit as good as the old method," he claims. "There's a lot less thinking involved."
That's a big factor since the traditional apprenticeship training is declining in the sheet metal shop. The sophistication of the machines seems to be addressing rather than fostering - the need for a workforce that, increasingly, is less skilled. Yet the demand for curved metal panels still calls for well-trained craftsmen that must respond to the intricate designs architects are creating.
A Roundabout Way
A magnificent house in Vancouver designed by Bing Thom, a local architect, utilized 7,500 square feet of zinc roofing and trim using curves, spheres, and an inverted airplane wing design that went from the exterior soffit, through glass windows and into the house's interior. It was only after Thom saw the expert soffit work of Flynn Specialty Metals, Vancouver, British Columbia, that he decided to carry the design into the house."That's about as hard as you can get in zinc work," says Ken Smith, owner of Flynn Specialty Metals. Founded in 1982, the company is Canada's largest independent roofing contractor. "Every panel was individually tapered on press brakes. He was pushing the envelope. Usually what I dream up, my shop can do."
Smith has been working with zinc - much of which is mined in Canada - for 20 years and will match his crew against anyone in the business. His company, which is in the midst of a merger with DHS, has gained a reputation for close collaborations with architects and executing tough jobs that others can't do. In fact, Flynn didn't win the original bid on the zinc-clad house and was brought in after the bid was reopened. Like many custom jobs he's completed, much of the work was priced as the project progressed. A tough sell for the average contractor, but Smith says his reputation won out over concerns of those dreaded change orders.
"Everybody wants to get value for money," he explains, "but when you get into the high-end stuff, (architects) don't want their name attached to a price. When you're dealing with complicated metal designs, they want it done right.
"I wanted to be in a niche market. We worked very hard in building a market."
Smith recalls one house that had $2 million in labor costs alone. With prices like that, the primary motivation is getting the job done right. He works closely with architects to anticipate changes and install it right the first time. Another curved metal panel job he got the call for was a reroof at a cost of $1 million dollars.
Flynn Specialty Metals has been exclusively in metal since 1985 and purchased its curving machine around 10 years ago. The machine has increased his stature in the design and contracting community while enabling him to better control costs, reduce prices and make the projects go more smoothly. In fact, he sees the usage of curved metal panels as a kind of blessing. "Curves are friendly in disguise," he says. "Sometimes straight lines are more difficult."
Report Abusive Comment