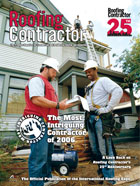
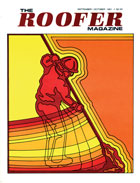
As part of Roofing Contractor's 25th anniversary, this is a glance back at some innovations, stumbles and events that give perspective to our current industry. There are many stories out there, and it's a challenge to dig so far back with all of the change that occurs, but here are a selection of updates and flashbacks on events that have shaped our industry. As we find more news about those that have graced these pages, we hope to keep readers informed with future updates on the projects, people and products profiled in the pages of Roofing Contractor.
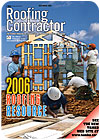
Just Venting
The first issue, a combined September/October issue which launched in 1981, discussed a new approach to a problem that still inspires debate and controversy: ventilation. Parker and Mudgett, and architectural firm in Fort Myers, Fla., capped a square residential house with vent that went around the entire top third of the roof. It was an effort to release heat and moisture from the crawl space in the days before double-paned low-E windows, radiant barriers and house wraps.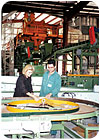
Deborah Currier Liftig, the first editor of Roofer Magazine, is seen with a technician from Vortex, an Italian firm that installed a $4 million tile production facility in 2001.
He has used the technique several times and often puts the air conditioning units in the crawl space on pitched roofs. The insulation is part of the roof deck as air enters the soffits, travels through the raised decking and out through the vent. Even though roof ventilation is part of the building code, there is still debate in Florida about circulating hot, humid air under the roofing system. The private home featured in the article still stands, albeit with a few additions.
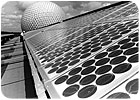
Tax credits available when this solar array was installed at the Epcot Center in 1982 are now back after a 20-year absence. The Energy Policy Act of 2005 gives a 30 percent tax credit for installing solar energy appliances and roofing contractors in California and Colorado are getting into the business. (Copyright Walt Disney Productions, 1982.)
Time to Reflect
In 1982, advertisements in The Roofer touted something new called a ceramic roof coating. The product was inspired by roof paint - something common in the South during the 1950s and 1960s - and was designed to improve thermal performance with the properties of ceramic granules. The space shuttle that would later launch from Cape Canaveral featured ceramic tiles on the bottom to insulated the craft from the intense heat during re-entry into the Earth's atmosphere.It turns out that the product's originator, Richard Ziebarth, was reading about those tiles when he had a "eureka" moment. Working with a chemist in the late 1970s, he formulated a white, durable coating that also acted as insulation. According to his son, Dave, the earliest use for the product was to insulate steam pipes, but customers in that market didn't buy much product. So the roof-painting contractor converted his fleet of trucks and built a plant in Inverness, Fla.
"We were going to be in any business that this ceramic technology would work on," says Dave Ziebarth, president of Insulated Coatings Corp. "I don't even think there was a reflectivity test back then. Emissivity was not something people said in 1982."
An early niche market centered on mobile homes, but the market expanded to include restoration of any number of roofs. In addition to avoiding the cost of a tearoff, the energy savings from a reflective roof were being recognized in the 1990s through Energy Star and other programs. Now building codes and tax breaks are feeding a huge growth in reflective coatings. Ziebarth has developed reinforcements and primers for coating EPDM roofs that fix seams, bring the thickness to 60 mils and make the coating reflective.
The market for reflective roofing has transformed from patch jobs into high-performing systems with 10-year guarantees. Benefits include saving money, energy and landfill space. In order to better promote the concept, the Reflective Roof Coating Institute held its first meeting at the International Roofing Expo in February. Even after all this time, Ziebarth is finding new applications for a bright idea.
"We're just getting started," he says. "Now that everybody is buying into it, we have to pay attention to quality in the industry. We've got roof consultants bringing us business. It's remarkable what we're able to do for the end user."
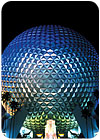
The Spaceship Earth appeared on the cover of our June 1986 issue. Disney's Imagineers report there have been no major renovations to the 180-foot geosphere since its construction in 1982. The exterior aluminum panels are supported 3 feet above the galvanized steel deck, which was roofed with 80,000 square feet of neoprene single ply and 48,000 square feet of neoprene flashing from Gates Engineering.
Fallingwater (Inside)
Famed architect Frank Lloyd Wright had numerous strengths, but roof details weren't one of them. His buildings' reputation for leaking roofs even reached his masterpiece, Fallingwater. Constructed in western Pennsylvania, this bold, angular construction was built over Bear Run creek. The flat concrete decks provided excellent views and dramatic lines, but were a bear to waterproof. Workers involved in the construction of the original house report mixing the concrete by hand and then shoveling it into forms, leaving the rounded tops on the parapets crooked but modern looking. The original roof was a built-up roof (BUR).In February of 1988, Roofer reported on a 60 mil EPDM membrane by Goodyear being installed. Several areas received pavers and lead flashing. Ten years later, the pottery terrace was reroofed with an inverted roof membrane system (IRMA) by W.R. Grace. The two-ply system with rubberized asphalt mastic was given a drainage mat to direct moisture towards newly installed drains.
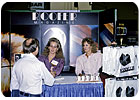
The magazine has always put its best face forward during conventions. Shown are Kimberly Maness, western region sales manager, and Peggy Hendrix, circulation director, in the late 1980s.
Focusing on Quality Control
When all tools were hand-powered and BUR was king, roofing was more of an art than a science. Sometimes three or four layers of some decent asphalt or coal tar can make up for shortfalls in design, training and even materials. But when oil prices shot up and the asphalt quality came down, single ply came in with a vengeance. Quality control became a mantra as fingers were pointed and new roofs were cut open to look for any voids between felts.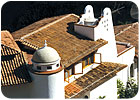
This roof in Puerto Vallarta appeared in the January 1995 issue as part of a series of photographic essays that date back to the magazine's earliest issues.
Endorsements trickled in over the years until, in 2001, the NRCA and the Asphalt Roofing Manufacturers Association (ARMA) worked together to produce a joint document that spells out standard practices needed to achieve a quality BUR or modified bitumen system. The booklet was released in 2004.
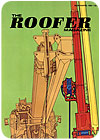
SIDEBARS
The Time Capsule
1982- The March/April issue included a feature article on using horses to tear off an existing BUR. They were used after union roofers refused to cross a picket line. The ponies were trained to pull 4,000 pounds on a sledgeboat and could even perform tricks. The issue also featured article on W.R. Grace's refusal to warranty BURs using fiberglass felts over Zonolite, a lightweight concrete deck. Organic and (with some limits) asbestos base sheets and felts could be still used.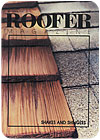
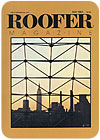
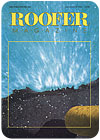
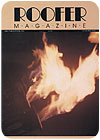
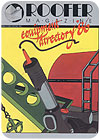

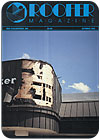
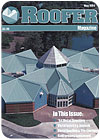

Report Abusive Comment