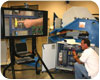
MetalForming’s OnLink™ service allows the MetalForming technician to remotely link directly with the controls of a contractor’s machine and communicate via a live, two-way video teleconference.
MetalForming Inc. owner Geoff Stone shared the story of an epiphany turned solution on a recent visit by Roofing Contractor to the firm’s Peachtree City, Ga., headquarters. MetalForming, founded in 1997, sells a variety of computer-operated machines used in the factory and on the jobsite for the fabrication of metal roofing and other building components.
Folding, slitting, shearing, and other machines furnished by MetalForming and others have long since revolutionized the production of metal roofing, roof drainage, and edge systems. Installing, operating, and maintaining this sophisticated machinery requires people with a highly specialized knowledge base.
Many roofing contractors operate these machines in sheet metal shops staffed by mechanics skilled in the craft of cutting and forming sheet metal, but not so much in computerized controls. Some roofing contractors and manufacturers have the scale to employ their own staff to install new machinery, train operators, troubleshoot, and maintain their machines and controls in-house, but most do not.
The solution to this problem, historically, comes from the firms like MetalForming that sell the equipment. They provide the installation, operator training, and maintenance support by way of their factory-trained technicians along with technicians working directly for the manufacturers of the machinery, many of whom are located in other parts of the world.
The Epiphany
Stone tells us he was taking a walk around the lake a few years back when an idea hit him. He was mulling a somewhat unpleasant conversation he had earlier with a contractor who had received the bill for technical services. The job was done, the machine was repaired and working, but the contractor was livid about the cost. The technician who solved the contractor’s problem had to fly to the customer’s location, spend a day or two, and fly back. The cold, hard reality is that travel expenses are brutal and they are constantly changing.Stone thought that with the Internet, video, and telecom systems it should be possible for his technicians to perform many of their functions without the expense and time required to travel to his clients’ sites. After years of development, MetalForming recently announced the introduction of OnLink™. The service couples the ability for the MetalForming technician to remotely link directly with the controls of a contractor’s machine, with a live, two-way video teleconference.
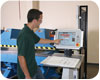
Remote Patrol
What all this means is with the OnLink service a machine may be put into service or maintained without a technician physically on site. Not only does this save dollars but it saves a tremendous amount of time. In the best of cases, having a technician on site requires scheduling and a good bit of travel time. With the remote solution the time to bring in the technician is reduced to practically nothing.When a contractor invests in a high-production automated folding machine, for example, it must be installed in the shop environment. Typically it takes a specialist on the site to do the job of making sure the machine is installed properly, tuning up the controls, and providing basic training to the operators. In many cases, the task can be handled from the MetalForming office with the contractor providing the “hands-on.” In addition to the technicians at MetalForming, the system has the capability of bringing the manufacturer online to assist with the same connection in Switzerland or Germany as in Georgia.
Operating any piece of metal-working machinery takes training, and operating a computer-controlled machine is no exception. MetalForming offers live and in-person training (expensive) or training via OnLink (not expensive). With the system, the technician can “capture” the controls of the device remotely and add the kind of step-by-step instructions they would give if they were in the shop. In a sense they are since their voice and image are on display. The two-way capability of the system allows the technician to see what is going on in the shop in real time while the contractor can see and speak with the technician.
Any machine with more than one moving part is going to require preventive maintenance. Most contractors who operate computer-controlled machinery will develop the in-house expertise to perform routine maintenance, but will require the assistance of factory-trained technicians. Same as with the installation and training, a live technician in your shop: expensive. Live technician connected via the Internet with two-way teleconference: not expensive.
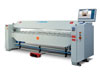
Simple Concept - Not-So-Simple Solution
It is the capacity to bring together the live link to the machine with the live two-way video teleconference that makes this system so unique - at least from the contractor’s perspective. From the perspective of someone taking an epiphany to a real-world solution, the development of OnLink has been nothing short of remarkable.The first system MetalForming developed to deliver machine-to-machine and the human connection via teleconference worked, but with a limited number of clients. Technical problems involving Internet connections and firewalls made the system difficult to operate in many locations.
For some time MetalForming has had a working relationship with the Georgia Institute of Technology. Georgia Tech students have participated in the building of the system as well as other systems developed by MetalForming, such as their Computer Integrated Roofing Manufacturing (CIRM™) Broker product. CIRM Broker was designed primarily for factory applications to reduce waste and enhance productivity.
The OnLink project was quarterbacked by MetalForming’s executive vice president and CIO, Bill Wilkins. While searching for solutions to the connectivity issues, Wilkins managed to attract the attention of some very significant players in the tech world. You would recognize the name of Microsoft, but perhaps not Level 3 Communications. Level 3 may not operate in the public view but it is recognized in the industry as a premier supplier of Internet, voice, and data delivery products. Microsoft was so intrigued by the OnLink concept that they invited MetalForming into its Technical Application Program (TAP), dedicating a team of engineers to assist with ongoing development.
Working with assistance from Georgia Tech, Microsoft, and Level 3, MetalForming managed to develop a system that took away virtually all of the technical challenges to connecting with all the machines they presently have in service in North America and beyond. Speaking of the systems used in OnLink, Wilkins said, “we developed a solution that turns stand-alone metal-forming machines into fully networkable, remote servicing systems.”
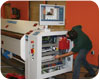
Getting Connected
MetalForming has set in motion plans that will allow users of their machines (as well as others) to connect via OnLink. MetalForming will provide all the software and hardware to get connected for installation, training, preventative maintenance, troubleshooting and repairs. New versions of some of their short and long folding machines will come furnished with the OnLink system that feature a “one touch” button located on the machine’s control screen. All the operator has to do to link up is to push the button and the machine calls into MetalForming and begins the video connection.The hardware may be sophisticated but it is not terribly expensive. While MetalForming and their partners have been developing OnLink, the cost of many components, such as HD video cameras, has come down considerably. The bandwidth required to power a system such as this is also reasonably priced and readily available just about everywhere.
While it took years to develop and a collaboration of a great engineering school and several world-class engineering companies, the process began like so many initiatives in the roofing industry: an entrepreneur with a problem who had the drive and determination to deliver a solution. Speaking of the system he dreamed of on a walk around the lake, Stone says, “We can offer a level of service that has never been provided by any machine tool company in the world.”
For more information about MetalForming, visitwww.metalforming-usa.com.
Report Abusive Comment