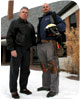
Mike Mathers of Roofing Technology Associates
and Tim Young of Royal Roofing check out the completed TruSlate project at
Walnut Creek Country Club.
(Photo by Karen McConnell.)
A country club can be a great place to find new business opportunities as well as a great place to play a round of golf. When Mike Mathers, President of Roofing Technology Associates in Livonia, Mich., spotted a business opportunity on top of his own country club, he was assigned the task of finding a solution to a tricky re-roofing job.
Mathers, who specializes in commercial and multi-family roof consulting, has been a member of Walnut Creek Country Club in South Lyon, Mich., for 10 years, and he’s served on the house committee for the last three years. He advised the board of directors that the main building’s 22-year-old cedar shake roof was worn out, and nothing could be done to extend its life.
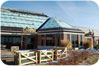
A roof consultant for more than 35 years, Mathers knew this specification would be a challenge. “There are a bunch of complications on this job,” he said. “First, we have a lot of attics in the steep-slope areas, and they are quite large. Also, the lines for the fire suppression system run through the attics, and they can’t be allowed to freeze. The attics are heated and unventilated, with no ridge vents, soffit vents or roof louver vents. So my first question was, ‘What type of replacement roof system are we going to use on this project?’”
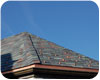
“I first saw it when a GAF representative happened to be in my office,” he recalled. The idea of using lighter-weight version of real slate had immediate appeal for Mathers, and he found several reasons to consider it for the Walnut Creek project, including:
• Durability. “You’re using actual, natural slate, so you’ll have a high life expectancy and a long-term life cycle,” said Mathers.
• Long-term warranty. GAF-Elk offers comprehensive warranty options. (See warranty at www.gaf.com for full details.) “It’s a great warranty from an established roofing manufacturer,” said Mathers.
• Weight. TruSlate roofs are much lighter than traditional slate roofs, noted Mathers. “Slate is a heavy product, and it’s very hard to retrofit an existing roof with slate. We had a structural analysis performed by an engineer and we found that the roof could support TruSlate.”
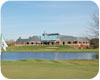
• Cost. “When push came to shove at the end of the process, the cost was very competitive with the other systems we could have used.”
He recommended TruSlate for the project in a three-color blend with 65 percent Greystone, 25 percent Eco Green, and 10 percent Vintage Plum. The board agreed. “I guess they realized over time that I knew something and went with my spec,” he said. “It was a bit of a stretch for a guy like me who’s been around for a long time. I’m very traditional and I seldom go with a newer system, so it was something different for me.”

The
installation included copper valleys and chimney flashing. Alpine SnowGuards
were installed over the entrances and exits.
In a TruSlate installation, UnderBlock UV & Moisture Barrier, made from a specially blended high-density polyethylene, is held in place with the slate tiles and with GAF-Elk’s patented TruGrip system, which uses high-quality stainless steel battens and hangers to lock each slate tightly in place.
Emily Cavanagh, Senior Product Manager, Designer Lifetime Shingles, TruSlate, and Decorative Exteriors for GAF-Elk, said TruSlate is an ideal fit for retrofit jobs that want to incorporate real slate.
“The TruSlate patented system combines real slate with GAF-Elk’s innovative hybrid technology resulting in a quick, easy slate installation,” she said. “It typically eliminates the expensive structural modifications that old-fashioned slate requires, making it a perfect candidate for both new construction and remodeling jobs. In fact, because the system only requires a 2-inch overlap of slate, contractors and property owners can use up to 40 percent less slate on a job to cover the same area.”
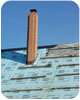
The roof of the country club is approximately
30,000 square feet, most if steep slope, with pitches as high as 12:12.
After installing roof deck protection and leak barriers, as well as drip edge and valley metals, the contractor installs the slates from the top down to minimize traffic on the slate. “Slates are simply slipped into place and snapped down tight,” said Cavanagh. “Should the need arise, slates can be replaced in seconds, without the tools. It’s so easy, any roofer can do it - not just experienced slaters.”
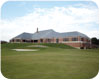
When the cedar shake roof had to be replaced on
Walnut Creek Country Club in Livonia,
Mich., a TruSlate system from
GAF-Elk was specified.
When the project was put out for bid, Royal Roofing of Orion, Mich., got the job. It was the company’s first experience with TruSlate, and GAF worked closely with Mathers and the crews from Royal to make sure the installation went smoothly. GAF let Mathers know about eight or nine projects he could visit, some while they were in progress. GAF also sent out their technical rep to the site to work with them on the job. “GAF also has excellent videos and an excellent installation manual,” said Mathers, who noted installation videos are available at www.truslate.com.
Royal Roofing’s foreman on the project, Tim Young, is the company’s slate and copper work specialist, so he adapted quickly to the TruSlate system. “I’ve done a couple hundred slate jobs, so it was easy to adjust to this,” he said. “Once everyone got the layout down, it was easy to install.”
The logistics of the jobsite were another matter, as the country club would be open throughout the course of the project. “It’s the nature of a golf course that people are coming and going all the time for golf, tennis, meetings and events, so a key decision was when to do the job,” Mathers recalled. They decided on the fall because golf traffic would be greatly reduced.

“Royal Roofing did a hell of a job,” said Mathers. “Tim Young, the foreman, was a very good communicator, which you don’t always get in the roofing industry. We met with the maintenance people at the club and set the scope of work for the day, made sure everyone knew what was going on each day.”
Attention to detail was the key. “They did an excellent cleanup job every day,” Mathers said. “They have a lot of brick patios, which were covered with tarps and plywood so no nails could fall between the brick pavers. It was a very good plan.”
The project was scheduled for completion in eight weeks but was wrapped up in seven, in part due to great weather. “Typically Mother Nature interferes with jobs in Michigan,” Mathers said. “We had tremendous fall weather.”
While club members might not have noticed the roofers at work during the installation, evidence of the finished project is hard to ignore. “I’ve heard nothing but raving positives from the membership,” said Mathers. “It was a significant expenditure for the country club, but it went as well as I could’ve hoped.”
Mathers conducted the final inspections himself at the end of each phase. After all, his reputation was on the line. “Obviously I have a lot at stake as a club member and a member of the housing committee and a member of my profession,” he said. “And everything went great. It was a great relationship with everyone from A to Z, all the way through. When you get projects that get completed this smoothly, with great communication and rave reviews, it’s fun to be a part of it.”
For more information about Roofing Technology Associates, visit www.rtaltd.com. For more information about Royal Roofing, visit www.royal-roofing.com. For more information about TruSlate, visit www.gaf.com.
Report Abusive Comment