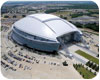
Photo by Aerial Photography Inc.
The mother ship of multi-use domed structures has landed in the form of the new $1.3 billion Dallas Cowboys Stadium in Arlington, Texas.
In particular, the roof installation by KPost Company of Dallas helped vault the space-age facility into the history books as the steepest retractable domed sports arena in the United States. “It looks like a spaceship,” KPost Project Superintendent Thomas Williams said. “There’s nothing like it anywhere.”
The materials and manpower alone give you a sense of the scope of the project, which involved 660,000 square feet of Sika Sarnafil roofing membrane (600 rolls of membrane at 391 pounds each); 1,620 five-gallon buckets of roofing adhesive totaling 8,100 gallons; over 350,000 screws; 10 miles of lumber; and 16 miles of structural silicone sealants on exterior glass. Sixty employees working 300 feet in the air took 91,635 man-hours to complete the work.
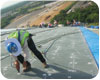
Safety was the top priority on the Cowboys Stadium project. All workers on the roof were tied off 100 percent of time, and material and tools were strapped down to prevent problems in the event of high winds. (Photos courtesy of KPost Company.)
The Game Plan
KPost Director of Operations Kelly Lea said the company was “very confident” when the bidding process commenced with the stadium’s general contractor, Manhattan Construction Company of Fort Worth, Texas. “We had a game plan,” Lea said. “Our confidence in doing the job right came out in the initial meeting. The Manhattan guys took it all in and just made the decision to hire us on our ability to deliver a quality roof safely and on schedule.”Lea secured Thomas Williams as the project supervisor. Williams spent 28 years in the Navy and was semi-retired before being asked to be part of the project.
“I can’t tell you enough how Tom’s Navy experience fell right into place for this project,” Lea said. “Because of his skill set, we were confident in his ability every day on the job.”
Williams noted that right before the stadium went to bid, KPost had successfully completed a 2,076-square re-roofing project for Manhattan Construction.
“They asked us to be involved in the Cowboys Stadium project,” Williams said. “We are not the biggest roofing company in Texas, but we had the team they were looking for.”
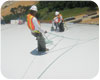
When Work Started
Work on the service building started in July 2007, although the “real roof work” began in March 2008, Williams said. The project was completed on June 1, 2009.Williams said the project took longer than expected because of changes in the construction schedule. He said the degree of difficulty, particularly with stocking and installation, as well as the schedule delay by the weather resulted in additional labor above what was originally anticipated. Having said this, Williams was proud to report that “all work was completed on or ahead of schedule in support of the opening of the stadium,” Williams noted, referring to the Cowboys NFL regular season opening game this month.
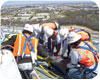
“It was a challenge,” said Ricky Harp, KPost Cowboy Stadium Project Manager. “In the end, after three years, we are very proud of everyone who worked on it.”
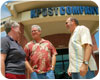
KPost’s CFO/Safety Director, Jayne Williams, talks about the stadium project with CEO Keith Post and President Steve Little. (Photo by Tom Watts.)
Safety First
KPost Director of Operations Kelly Lea said all workers were tied off 100 percent of the time during the roofing project.“Safety was the most important thing,” Lea said. “I relied on Tom (Williams) to make sure our crews followed all safety guidelines. Cuts and bruises were amplified.”
Williams said the wear and tear on the body was brutal on crews after dealing with constant loading of materials and extreme Texas weather conditions.
“We had to figure out logistics of where to be tied off, how to get up and down, and facing 30 mph winds and 100-degree days with 95 percent humidity,” Williams said, noting the slope of the roof required that all material, tools and generators were anchored with straps and wood blocking.
“The logistics were a nightmare,” he said. “The slope of the roof made it very difficult.”
Williams said 200- to 240-foot safety lines were purchased from Superior Equipment in Fort Worth, Texas. The majority of harnesses were made by Fall-Tech and the roof anchors were made by Guardian Fall Protection. A full-time safety monitor (Andy Bruruman) was also on site during stocking and roof installation.
“You can’t overestimate the amount of labor to stock the roof,” Williams said. “We used 10 men to stock 80 squares a day.”
KPost safety compliance coordinator Luciano Perez participated in weekly safety committee meetings for the stadium project, as well as teaching a 10-hour OSHA class for crews.
“It is a passion to interact with people and teach them safety,” Perez said. “I have fun doing what I do. This is serious business. The gravity does not forgive the employee. The bottom line on this project: 100 percent tied off with harnesses and personal fall arrest systems.”
Project Requirements
The size of the project was monumental and the right products needed to be used. Enter Rick Chappell, an account specialist for Sika Sarnafil who used terms like “sustainability” and “longevity” to define his product.
“Ricky Harp calls me and said they have a large project,” Chappell said. “I saw where the architect was HKS Architects, which was the same architect I worked with on the American Airlines Arena in Dallas a decade ago.”
Chappell said he was on the jobsite about 10 times during the single-ply installation. “I can sell it, but it’s the roofing crews that make it as good as it looks,” he said. “I’m amazed at what these guys went through during installation at 300 feet in the air.”
KPost installed about 6,600 squares of fully adhered 60-mil PVC roofing membrane on the stadium roof, which included a small service building and restroom building (37 squares), two mid-level roofs (192 squares), eight clerestory roofs (29 squares), two low roofs (869 squares) and the fixed dome (5,462 squares).
One of the mid-level roofs and both low roofs were structural concrete decks, while all other roofs were metal deck with the dome being an acoustical deck. The low roofs, mid-level and clerestory roofs were fully tapered systems.
The dome roof consisted of acoustical insulation installed in the flutes of the metal decking; Sarnavap fully taped for a vapor barrier; 1.8-inch thick polyisocyanurate; 1/4-inch DensDeck Prime; and fully adhered 60-mil PVC G410 Sarnafil membrane. The system was attached using 31/4-inch Sarnafil screws and plates per FM Global requirements.
The 60-mil PVC membrane was fully adhered using Sarnacol 2170 adhesive, and the seams were heat welded.
“Sika is the Cadillac of single-ply roofing,” said Williams, noting the fastening pattern was a minimum 16 fasteners per 4-foot by 8-foot board per FM Global requirements.
Williams said the 1.5 inch iso and thicker DensDeck was also used in corners exposed to higher wind uplift. Pressure-treated lumber was installed at all perimeter edges and areas of transition using stainless steel screws, he said.
KPost Company worked with Haley Greer, a glass subcontractor, to caulk and wet glaze all glass areas of the stadium through its waterproofing division. KPost also worked in concert with BirdAir, who installed the fabric on the retractable roof.
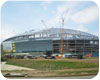
Moving and Securing Material
The general contractor, Manhattan Construction, made sure KPost had an area for material to be secured to the roof.“We were required to move the material on several occasions due to paving of parking lots,” he said. “All of the Sarnafil G410 membrane was produced in a single run at the beginning of the project and stored in a local warehouse until needed at the jobsite.”
Williams said KPost used a 300-ton crane from Crocker Crane in Irving to load material. The crane was outfitted with a 380-foot boom. However, a hydraulic winch was required to pull material to the top of the dome.
“All material and tools had to be strapped down due to the forces of gravity and high winds frequently present on the dome,” said Williams, who noted both the Sarnavap and G410 membrane came in rolls, so unless the material was strapped down, it could easily roll off the roof - which it never did.
“With G410 membrane rolls weighing in at 391.5 pounds, we had to be especially careful when handling these items,” Williams said. Rolling out a roll of this membrane on a standard flat roof requires one or two men, according to Williams, but handling a roll of membrane on the dome required up to eight workers.
Also, because much of the roofing was completed during the summer months in 2008, the Texas daytime heat resulted in crews starting work about 4 a.m.
Manhattan Construction Superintendent Richard Duchesne said the most difficult part of the project was getting the structure watertight. “But when we did, she came alive,” Duchesne said of Cowboys Stadium. “It’s the greatest feeling in the world to know this one-of-a-kind structure is open for business.”
KPost President Steve Little said he along with CEO Keith Post and CFO/safety director Jayne Williams, the officers of KPost, are just very small part of the reason for the new Cowboys Stadium success.
“I would say it was a job well done and that our employees made the difference,” Little said. “We performed as a team with an eye on safety, quality and value.”
“We lead by example,” owner Keith Post concluded. “We plan, execute and manage everything we do. There is not a ‘no’ and ‘can’t do’ in the minds of any KPost employee.”
“We have a great team at KPost,” stated Jayne Williams a diehard Colts fan, “and we’re proud to have roofed Cowboy’s Stadium, the new home to America’s team”
Sidebar: Cowboys Stadium Roof Project
General Contractor: Manhattan Construction Company, Arlington, TexasArchitect: HKS Inc., Dallas
Roofing Contractor: KPost Company, Dallas
Roofing Consultant: WJE Inc., Irving
Roofing Manufacturer: Sika Sarnafil Inc., Houston
Roofing Subcontractor: Crocker Crane, Irving