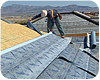
The Roofing Company of Las Vegas installed Tarco
PS200 HT self-adhering underlayment on a major housing construction project
outside of Las Vegas. (Photos courtesy of The Roofing Company of Las Vegas.)
Residential roofing in Las Vegas has its own types of challenges. In the summer, temperatures routinely soar into triple digits, and temperatures on rooftops are especially scorching. That can be a problem when installing self-adhering underlayments, as roofers from The Roofing Company found out the hard way on a major housing construction project outside of Las Vegas.
Founded in 1947, Hunt Building Company Ltd. is a privately owned, full-service construction company with headquarters in El Paso, Texas. It has contracted to build housing for the Airmen of the Nellis Air Force Base and their families. Under the contract, Hunt will build 532 structures, including both duplex and single family, for a total of 1,180 units. The family housing will be owned and operated by Nellis Air Force Base Properties, LLC, as part of the Air Force Privatization Program, which allows the services to leverage appropriated construction funds and government-owned property to attract private capital to improve military housing.
The old housing at Nellis AFB dates back nearly a half-century. It will be demolished and replaced with the new housing, including about 25,000 squares of new roofing. The roofing specifications call for a self-adhering underlayment under the tiles, to ensure a long life for the buildings. Hunt Building Company does not cut corners when it comes to quality of installation and materials; hence, a self-adhering underlayment was specified for use beneath the concrete tiles rather than the No. 30 felt that is commonly specified under tile roofs for housing in the Las Vegas area. These new homes are expected to last 50 years or more.
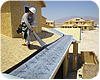
Trouble at the Start
The problem was that the initial brand of self-adhering underlayment just couldn’t take the heat. Construction began in August 2007 and, according to Tom Pavalko, the project manager for The Roofing Company, the roofing contractor for the project, there was trouble from the start. “We were using a different product at the beginning,” Pavalko said, “and the release-film backing wasn’t coming off. It was real sticky and was coming off in pieces.”The sticky release film was a serious problem that The Roofing Company struggled with through 12 duplex buildings (24 units) before changing over to another product. There were other problems, too. “After you finally installed it, when you left it overnight, it would get a fine dust on it, and the traction would be gone,” Pavalko said.
Fortunately, Guy Bennallack of The Roofing Company is a hands-on owner who is always on the lookout for new and better roofing products. He has been researching new products ever since 1984 when he took over the family-owned company, which has been doing business in the Las Vegas area since 1963.
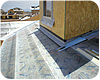
The Roofing Company of Las Vegas completed the roofs on these homes
for residents of Nellis Air Force Base and their families. (Photos courtesy of
Pinnacle, The Landings at Nellis.)
“I was instantly happy with it,” said Pavalko. “Compared to what we had been using, it was like night and day. It has good traction, it’s real easy to peel off the backing, and it allows you to set it in place. You can move it around a little before it adheres.” According to Pavalko, you can move the PS200 underlayment around and get it aligned. But after a day, it really adheres. “Nobody is going to move it,” he said. “The other product, once it touches you can’t move it. With this product you can get the laps nice and straight.” The PS200 product has a polyester surface that provides excellent traction. The slopes of the roofs are 5/12 to 6/12 and 4/12 in some places.
“It’s important to have good traction and we really like the walkability on the PS200 underlayment,” says Pavalko. “We haven’t had any wind related damage but it does get windy up here. Safety equipment includes ridge runners and ropes. The No. 30 or No. 40 felts could be damaged around the eaves or the drip edge. This product adheres to it and so there is no damage.”
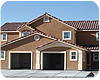
The Dry-in Phase
Pavalko described how he has two two-man crews who “run the underlayment” in the morning when it is relatively cool, which in Las Vegas means around 85 degrees Fahrenheit. The roof uses a full batten system for attaching concrete tiles. Once the underlayment is installed, the “dry-in” phase of construction begins and the other trades stucco and paints the exterior walls of the building.“We don’t install the tiles until the other work is done. It’s better to avoid overspray on the tile,” he said.
“Also, a lot of scaffolding needs to be moved around, which would otherwise damage the tiles, so we install the tiles last.”
Pavalko reported that the PS200 is very durable. “If some stucco gets on it, it comes right off.” And it is not a problem leaving the underlayment exposed while the exterior work is done. PS200 has superior UV resistance and provides full moisture protection. The construction schedule is such that the exterior work is completed and the tiles can be installed within 45 days or 60 days at most. Since PS200 is rated for 90 days of exposure, there is never a problem with exposure limits.
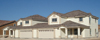
Built to Last
The two two-man crews each can do 48 squares a day. The duplexes are 65 squares and the single-family homes are 45 squares. After installing the underlayment, they staple down the batten and the loaders stack the tiles on the roof. Then the two crews go onto other buildings. After the stucco and paint are put on the building, they come back and install the tiles. They drive 2½-inch nails through the tile, batten and underlayment, down into the roof deck. The nails penetrate through the top compound, the fiberglass reinforcement and the bottom compound of the underlayment. The sticky compound on the bottom-side is a modified bituminous material that easily seals around the nails.“This is a high quality roof that is meant to last,” said Pavalko. “The Hunt quality assurance people come around and look at our work and have nothing but positive things to say about it. They like the fact that it is easy to walk on.”
“I think it is nice what they are doing for the active military,” he concluded. “These are nice houses.”
For more information, visit www.tarcoroofing.com.