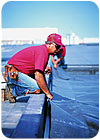
When the “green movement” started out, it was widely viewed as a quaint notion being pushed by lefty tree-huggers and New Age hippie-types. But then somebody figured out that there was money to be made, and suddenly the message has gotten stronger and louder and more ingrained in mainstream thinking. The global warming flap notwithstanding, there is plenty of agreement that protection of the environment is an important issue. Who’s pro-pollution? But, as with most other things in life, there are tradeoffs, and when it comes to single-ply roofing systems, that idealistic green bandwagon has just pulled up to the corner of realism and practicality.
A properly manufactured and installed fully adhered single-ply roofing system can provide outstanding protection for a building and its contents. There are those who will tell you there is nothing better in certain situations. One of the keys to their success is the use of high-quality, optimal-performing bonding adhesives, and one of the keys to the success of these adhesives is the solvent they contain. There is a lot to like about these systems and the solvents they employ, and, at the same time, there is plenty to be concerned about.
“These solvents typically are toluene, hexane, acetone and sometimes xylene, and all of them have health implications - for the people doing the installation and the people occupying the building,” notes Phil Georgio of Chem Link Inc. “These solvents have been designated by the EPA (Environmental Protection Agency) as air pollutants, and of course, they are very flammable. The EPA had a rule, that was to take effect in 1999, that solvent-release systems would be limited to 200 grams of VOCs (volatile organic compounds) per liter. That would have been the end of solvent-release systems as we know them in the roofing industry. The industry argued vehemently against this, and with the EPA in a state of transition at that time, that ruling was put on the back burner and never employed.”
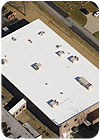
White roofing is no small part of the green movement. (Photo courtesy of Mule-Hide Products Co.)
Trending Up
While there is no national directive prohibiting solvent-based adhesives, California (surprise!) has had one for some time, and as you move east, there are more and more local prohibitions being established. Accompanying this increased scrutiny is the seemingly counter-intuitive fact that the popularity of fully adhered roofing systems actually is growing stronger in the face of these concerns. “Certainly on the EPDM side, the trend toward fully adhered systems has continued unabated,” says Michael DuCharme of Carlisle SynTec Inc. “It’s the stability of the system. Everything is completely affixed to the building and not moving. With the storms we’ve experienced in recent years, there’s an increased focus on getting a higher performance roofing system. So over the last half-decade, there’s been a steady increase in adhered systems.”Firestone Building Products’ Jim Jannasch concurs, saying, “Fully adhered systems have been growing substantially over the past several years, while mechanically attached systems are down. Fully adhered systems now exceed 35 percent to 40 percent of the market.”
Jannasch cites some of the reasons for this growth: “Over the years, Factory Mutual has changed its fastening requirements, so with a mechanically attached system, you have probably 30 percent more fasteners, and that immediately converts into increased material and labor expenses. Also, the use of spray equipment to put down the bonding adhesives is much faster than the traditional dip-and-roll-out-of-a-pail method. And it used to be that fully adhered systems were limited to 10-foot wide panels; now contractors routinely install 30-foot wide panels. The combination of those three things really has pushed adhered over the past 10 years.”
“There is a shift toward fully adhered roofing systems because of their strength and durability, and I think it will keep growing,” says Georgio. “Ballasted roofs are being prohibited in high-wind areas. Single-ply sheets have gotten bigger, impacting mechanically attached systems because of the increased stress being placed on the screws in the battens. Heat-welded systems use a lot of electricity, and don’t completely eliminate the possibility of a fire. And it’s easier to warrant a fully adhered system.”
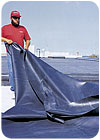
The health and safety of crew members is always an important issue. (Photo courtesy of Firestone Building Products.)
Health and Safety
So these solvent-based systems have much to offer that appeals to those looking for maximum performance in roofing systems. On the flip side of the coin are concerns that the detrimental aspects of the fumes associated with these products outweigh the adhesives’ benefits. They’re flammable, noxious and mostly unkind to the environment.Beyond the risk of fires, there is the human element to consider. The health and safety of the employees doing the installation is always a key concern. “Up to now, OSHA (Occupational Safety and Health Administration) hasn’t started monitoring employees for exposure to the solvents. They did that with asbestos,” reminds Georgio. “If that happens, and they start to look at what the crew members are exposed to over an eight-hour shift, there might be some real concerns over neurological damage and liver damage and things like that. If this was something that was going on in a production setting in a manufacturing facility, OSHA would be all over it.”
Additionally, solvent-based products aren’t a whole lot of fun to get from point A to point B. “Transportation certainly is an issue,” says DuCharme. “There are fewer HAZMAT drivers, and there’s potential for increased regulation there.”
And go ahead and ask your insurance agent what he thinks about all those red-labeled cans in the warehouse.
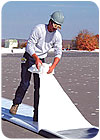
Peel-and-stick systems offer an alternative to the liquid adhesive systems. (Photo courtesy of GenFlex Roofing Systems.)
What to Do?
“People are looking for alternatives to the traditional solvent-based adhesives in certain applications,” says David French of Versico Inc. “There are situations where you need something other than a solvent-based adhesive, and manufacturers want to make sure that they have those options available, so they are working on developing alternatives that provide the same quality of performance without some of the unfavorable characteristics of the solvent-based adhesives. Legislation obviously is a big driver, but application is a factor, as well. For instance, as more and more roofs need to be reroofed while occupied, more and more people will look to the available alternatives.”“There is a whole series of options to solve the issue, depending on how onerous the regulations get,” explains Carlisle’s DuCharme. “The spectrum ranges from where we currently are with solvent-based products to what we call low-VOC California-compliant products, which still have some solvent in them, but meet the necessary requirements. On the next level of environmentally friendly products are the water-based products. With the water-based products, there is a tradeoff to a degree in performance and a tradeoff in user-friendliness. And the window in which you can successfully use water-based products is narrower. All this limits the amount of work that can get done. And we all know that labor is one of the tightest resources in the industry. What we have when these regulations come into play is lower productivity on the roof at a time when we’re all trying to step up our game because the volume of roofing being put down every year continues to grow.”
Tim McFarland of Mule-Hide Products Co. says that, while the industry is moving toward water-based products, that movement might take a while. “Contractors can be pretty set in their ways, and when they know a good thing, they like to stick with it,” he says. “It can take a while to get them convinced that going in a different route will be of benefit to them. Sometimes, the learning curve is quick, and sometimes it takes a while. The solvent-based adhesives are very forgiving products. The water-based products are more sensitive to temperature and humidity, and they a little more temperamental to work with. But on the other hand, the contractor can go to the building owner and say, ‘I’m going to put down this fully adhered roofing system for you, and you won’t have to worry about fire or any odors coming down through the building because we’re using a water-based product.’ Roofing contractors can present it as an upsell by removing that concern for the building owner.”
“When they first came out, the water-based products were much more expensive, and it was difficult to pass that on,” McFarland explains. “As the products are being refined, the costs are coming down. They’re getting closer. As time progresses, the technology is getting better and better.”
Chem Link’s Georgio adds, “Manufacturers are working to reduce the solvents to where they fall into the 20 gram-per-liter range. But if you’re going to do that, you might as well go the whole nine yards and just make them solvent-free, because it’s hard to dissolve materials with only 20 percent solvent content in the adhesive. There are solvent-free contact cements that are in the developmental stage. I’d say by the next national trade show, you’ll see a commercial solvent-free contact cement for EPDM that will be cost-effective.”
A Matter of Geography
Not that there’s any deadline looming. Versico’s French says, “Certain areas of the country are becoming more restrictive as far as what types of adhesives can be used, but I don’t see it as something that’s going to take over nationwide or industry-wide at this point - at least not in the near future.” And that’s buying the industry’s R&D people time to come up with the products of the future.“These things start out west and gradually make their way east,” says Carlisle’s DuCharme. “California is the driver in restricting the level of VOCs in these roof components, and their emission into the environment. It’s moving at a slower rate than we might have predicted years ago, but it is, indeed, moving. The area that holds the most promise for the future is the peel-and-stick membrane technology. It essentially removes the liquid adhesive from play,” he explains. “The adhesive is factory-applied at a consistent thickness in controlled conditions. On the roof, the roofing crew simply peels off the backing and sticks the membrane to the substrate. So, with regard to the trade-off issue, that gives us a chance to get back to optimum productivity and user-friendliness, while maintaining approximately the same level of performance as you’d get with a liquid adhesive.”
“The technology is available to do it,” insists Georgio. “The question is to what extent the federal government and local governments are going to insist on it. I don’t think people are going to move to it voluntarily - unless they have some other reason to do so besides the air-quality issue.
“If we could make a 100 percent-solids material that was less expensive than solvent-release, people would go to it in a minute,” he offers. “The reality is, we’re not that far away from it. It’s just that everyone looks at cost per gallon and not cost per square. Installed cost with solvent-free systems is not a bad number. For instance, if you look at the recent increase in the cost of asphalt, everyone thought the world was coming to an end, but people still are installing asphalt-based roofing. If you’re talking about a slight increase in the cost of the adhesive, remember - the adhesive only represents maybe 10 percent of the cost of the roof. If the cost goes to 11 percent in order to be VOC-compliant, that’s not the end of the world either. And when you consider the cost to the community and the cost to the health of the installers, how do you equate that to installed cost?”
Driving Forces
While building owners, architects and specifiers are, indeed, joining the green movement and trying to be good stewards of the environment, they also have the accountants in their ears. Firestone’s Jannasch reminds us, “When architects or owners want low-VOC products used, and the contractor lets them know that it’s going to cost X amount of dollars more for the adhesives, they’re often pretty quick to back off on that.”But the industry seems resigned to that fact that some day in the not-too-distant future, the solvent-based products will be a thing of the past, going the way of asbestos shingles and staple guns. “Eventually, it’s going to happen,” says Jannasch. “It’s just a question of how long it’s going to take. I mean, California has been requiring this for 15-plus years or something like that. It will have to be legislated, and I don’t think it’s going to happen anytime soon. Right now, the focus is on white roofing, which is easier to address.”
The pressure is going to come from three fronts, predicts Georgio. “The building owner and architect community definitely is becoming more inclined to go green. Regulatory bodies will demand compliance - much like how kettles are banned in many areas. Thirdly, imagine if one or two major roofing manufacturers say they’re going green, and provide the leadership to bring a complete change to the industry. They’re green, they’re competitive, and they can operate everywhere in the country, and the insurance rates go down. That will give them such an advantage, that the rest will get in line to follow.”
Remember that it wasn’t all that long ago that roofing contractors were reluctant to try those crazy rubber sheet systems because they were unproven and cost so much. Manufacturers were able to keep working to bring down the price while improving performance.
“It’s an evolution that we’ll all have to deal with, and more and more people are willingly getting on the bandwagon,” says McFarland. “And that’s a good thing.” He also points to the LEED program as another driving force. The Leadership in Energy and Environmental Design Green Building Rating System is the nationally accepted benchmark for the design, construction, and operation of high performance green buildings. “As LEED grows - and it is growing - it’s going to have a significant impact in pushing along these environmental issues,” he stresses.
In all likelihood, most fans of the solvent-base fully adhered single-ply roofing systems will continue to go with them wherever possible until they’re absolutely abolished. Others will be inclined to start working with alternative systems to find out what works best for them in specific situations. A handful might commit totally to the green thing. God bless them all.
In the meantime, it is heartening to know that there is some time, and that the roofing industry boasts plenty of resources to make sure that new technologies are in place when the time comes for a change. Roofing contractors will be insisting on nothing less.
Report Abusive Comment