
Christen Detroit's contract for the North Terminal Redevelopment included installing the parapet walls. (Photos by Bobby Alcott)
Once Metro Airport’s Edward H. McNamara terminal was completed in 2002, the Wayne County Airport Authority moved forward with the next round of improvements, which centered on the North Terminal Redevelopment Project. The new North Terminal, which will replace the airport’s aging Berry and Smith terminal complex, is an 800,000-square-foot terminal and concourse that was designed to feature 26 gates and a Federal Inspection Station (FIS) to accommodate international flights.
Two Michigan-based contractors, Walbridge Aldinger and Barton Malow Co., teamed up to serve as the general contractor of the project under the name of Walbridge Barton Malow (WBM) LLC. The roofing contractor chosen by the joint venture was Christen Detroit Roofing, Detroit, a division of Fred Christen & Sons Co., Toledo.
The roof design called for approximately 500,000 square feet of fully adhered 60-mil GAF EverGuard PVC membrane over two layers of 1.5-inch isocyanurate insulation, which was mechanically attached to the structure’s steel deck.
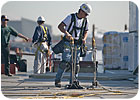
Workers from Christen Detroit Roofing mechanically attach insulation to the deck of the roof atop the new terminal at Detroit Metropolitan Wayne County Airport using AccuTrac tool from OMG Roofing Products.
Safety First
Jim Brown, division safety director for Christen Detroit, was in charge of safety on the project. The safety program was instrumental in getting the bid, noted Brown, who wrote the safety program and helped bring everyone up to speed at pre-job meetings. Employees outside of the warning line 10 feet from the building’s edge were fully tied off 100 percent of the time, and Miller DuraFlex harnesses were used as part of the personal fall arrest system. "With fall protection, the anchor points are key," Brown said. "What’s 100 percent tied off mean if the anchor point isn’t secure?" The plan called for the use of the PR 600 Mobile Fall Protection cart from Protective Roofing Products Ltd., which the company has used for seven years. "Ease of use and ease of movement means the workers can spend more time at the edge working," he said. "And the fact that we don’t have to install and engineer temporary anchors means we save time."One key component of the safety plan was constructing an exterior stair tower, built from scaffolding, which eliminated the need to reach the roof by ladder and eased the transportation of workers and material to the rooftop. "We’re always looking to make it better," said Brown.
When Roofing Contractor visited the jobsite in May, the only problem was the Christen crews were so far ahead of schedule they found themselves waiting for other trades to finish the structure. "We can’t get them to put the building up fast enough," Brown said.

Workers install tapered insulation and cut holes for the drainage points.
The Installation
The sheer magnitude of the job presented the obvious challenge, and proper staging of materials and efficient installation procedures were critical due to concerns about wind. "The job is staged as we go," said Claude Garrett, general superintendent, Christen Detroit. "In the beginning, we’d get deliveries about once a week. We have a holding lot, and we put material up with our own crane."Wind was a concern, noted Garrett, and debris couldn’t be allowed to blow off the roof and get sucked into a jet engine. "You’re in the middle of 90 acres, and the wind really gets going, plus there is a lot of jet wash," he said. "You have to make sure what goes up on the roof stays on the roof - keep the material on and the debris off."
The right equipment was also essential to the job, and the folks at Christen Detroit had high praise for the AccuTrac tool from OMG Roofing Products. The OMG AccuTrac is an automated insulation attachment system designed to provide the lowest installed cost for mechanical insulation attachment. In one step, the insulation plate is placed in position by the AccuTrac tool as the laborer drives the fastener, allowing one worker to do a job that normally would require two people.
"AccuTrac saves time and labor," stated Rob Owens, foreman, Christen Detroit. "When you have one worker laying down the plate and another screwing it in, you not only have two workers in the area, you have extension cords that might move the plates. It saves a lot of time. Plus, it handles a variety of screws from 2 to 6 inches, so it’s easy to work with saddles."
"It really saves on the back, and it goes as fast as you can feed the screws," Garrett said. "I can do four seams with AccuTrac in the time I can do one without it."
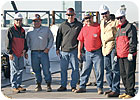
Checking out the job’s progress in early May are (left to right) Mike Binsfeld, national accounts manager, OMG Inc.; Jim Brown, safety director, Christen Detroit; Dave Thompson, senior estimator, Christen Detroit; Claude Garrett, general superintendent, Christen Detroit; Josh Kelly, marketing manager, OMG Roofing Products; and Pat Cherry, field technical sales representative, OMG Roofing Products.
Coping With Problems
Dave Thompson, senior estimator for Christen Detroit, knew that the scope of the project, the winter start and the wind conditions would be factors to consider when he bid the job, but he was on the lookout for design-build problems along the way."There were some typical problems that you routinely encounter in the field," Thompson said. "For example, we had to trim the deck back to install the parapet walls." He explained that the deck had to be cut back at the perimeter, as the design called for the parapet walls to be installed on the structural steel, but the deck as initially installed by other tradesmen reached the roof edge.
"The iron workers paid us extra to cut 5 1/2 inches off of the deck," Garrett said.
The roof also features acoustical decking in the areas over exposed ceilings. In the areas with acoustical decking, crews installed fiberglass fire-retardant mesh and filled the deck with 21/2 inches of fiberglass. They had to skin over those areas with 4-foot by 10-foot sections of sheet metal to hold the fasteners. They balanced out any uneven areas as they applied the insulation, resulting in a uniform surface.
As this issue went to press, Garrett estimated the job was about 90 percent complete. He pointed out that the company had gotten the go-ahead to do other roofing work at the site, including an addition amounting to another 100 squares that had been added to the terminal building.
Proper planning, efficient installation procedures, and proper equipment are all essential with any project, but everyone interviewed for this article pointed to safety as the most important concern. "Safety is part of your competitive edge," said Thompson. "Your safety performance is a key factor."
"No write-ups, no violations, no injuries - that’s pretty impressive with a job of this size," commented Garrett. "We owe it all to Jim Brown, who wrote the safety plan. The general contractors looked to him for safety advice for the entire project."
As he looked forward to wrapping up this phase of the project, Garrett noted that despite the high-profile nature of the job, the installation up to that point had been routine. "Just another day at the office," he said. "It’s the half-mile walk I will remember most. Usually we’re up somewhere on a small square box, so it was a longer walk than usual every morning."
Report Abusive Comment