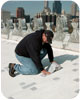
Stopping leaks is part of any roofing contractor’s job description. Other common tasks include securing edge metal and repairing cuts and failing seams in a variety of low-slope roof systems. Chris Margarites, the president of EternaBond, says his revolutionary roofing tape can be the answer to all of these problems - and then some.
Its ability to be used with a variety of roofing surfaces, including EPDM, TPO, most aged PVCs and Hypalon - as well as gutters, copings, edge metal, skylights, ductwork and other roof accessories - has made EternaBond standard equipment for many roofing contractors.
Charlie Von Plato, owner of Metal Roof Specialty Coating/US Roof Coaters (www.usroofcoaters.com) in West Chester, Pa., was one of the first contractors to use EternaBond, and he has made the product an integral part of his business strategy.
“We’re roof coating contractors,” said Von Plato, who specializes in commercial and industrial work. About a decade ago he read that Margarites was selling packages for repairing roofs on trailers, and he bought some and tested it out. Von Plato realized that the tape would be beneficial in large commercial and industrial roof repairs. “Now I had a product that I could use on the seams, and I could coat the material and ensure a watertight roof,” he said.
Von Plato first used it to patch holes and seams in metal and old Hypalon roofs before coating them, but soon expanded its use to parapet walls, asphalt roofs and EPDM roofs. Large holes and gaping seams are easy to spot on EPDM roofs, said Von Plato, but power washing the roof helps reveal small holes, cuts and minor seam problems. “Big failures are easy to see,” he said. “Small ones are hard to spot.”
He’s found it saves time and labor on EPDM roofs when the adhesive holding the seams fails. “It’s the only thing I’ve found that sticks to rubber,” he said. “All you have to do is wipe that area with the rag if you have a bad seam. I use a wet rag, a dry rag, put on EternaBond, use a roller and it’s done. It’s a great product.” He uses a fabric-backed version called WebSeal that is designed for use with roof coatings.
For metal roofs, the company power-washes the roof and tightens and replaces fasteners as needed. A rust-inhibiting primer is sprayed on the roof, and seams are sealed with EternaBond.
“With EternaBond, just peel and stick and you’re done,” he said. “It forms real nice, it’s easy to work with, it holds extremely well and it’s instant waterproofing. Then we apply two coats of the coating.”
Since he is a certified applicator, the company offers a 10-year labor and materials warranty. “I’ve been restoring roofs for a long time, and it really is what roofing will be in the future,” said Von Plato, who has worked for other contractors on roof restoration jobs.
“It’s an interesting business, and Chris’ product has made it easier - flat out easier.”
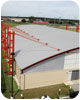
Approximately 30,000 linear feet of RoofSeal was used to repair the seams on the metal roof at the Niles West High School field house in Skokie, Ill. (Photo courtesy of EternaBond.)
Standing Up to Standing Seam Roofs
Mark Moran is vice president of Knickerbocker Roofing (www.knickroof.com), a fifth-generation family-owned business headquartered in Harvey, Ill. EternaBond played a large role in one of the company’s toughest projects, the field house at Niles West High School in Skokie, Ill.“It was a standing seam metal barrel roof, and for all of the seams - both the standing seams and the transverse seams - we applied the EternaBond tape,” Moran said.
“We chose to use RoofSeal with the gray UV-stable backing. It really blended in with the standing seam roof, especially from a distance. This allowed us to not have to coat it.”
The company power-washed the roof and applied an estimated 30,000 linear feet of EternaBond. Crews used 8-inch rolls with the peel-off release liner pre-slit to fit the seams and rolled backwards, allowing installers to roll it out, pull off part of the release liner, butt it up against the seam and apply the tape to one side while the remaining part of the tape was still protected by the liner. After the crews had installed the tape on one side of the seam, they would work up and over the seam to the other side. (A video of this application is available at the company’s Web site,www.eternabond.com.)
“The people at EternaBond worked closely with us on the project to make sure it went as efficiently as possible,” Moran said. “They back-rolled the tape and changed how they packaged it for us, and it just moved right along.”
“We use EternaBond for a variety of purposes,” said Moran. “We use it to patch core samples on single-ply roofs, for minor repairs, flashings, and overnight tie-offs.”
Moran noted that it is often used at parapet walls and flashings on a temporary basis while the company looks to make long-term corrections or a complete reroof.
“It’s unique,” he said. “The microsealant that’s on it - it sticks. Our guys in the field know it’s going to stay on.”
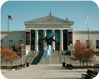
The John G. Shedd Aquarium was built for the Chicago Exposition in 1892, and before its renovation in 2004, the roof was a patchwork of different systems installed over the years. (Photo courtesy of EternaBond.)
Securing Edge Metal
David Susi is president and CEO of RSI Roofing (www.thinkrsi.com) in San Diego. “We specialize in commercial recover, so we have a lot of opportunities to use EternaBond,” said Susi, a 30-year veteran of the industry. “About two years ago we made it part of our standard material list on our crews.”Stacia Whitehurst, head of RSI’s maintenance division, noted that RSI’s crews use it on ductwork, A/C units, valley areas and pipe flashings, as well as roof leaks. “It’s easy to apply, and not labor intensive,” she said. “We started using it in a few patches where the warranty was out of place, such as a slice in a single-ply roof. We’d clean it, prime it, and use EternaBond.”
Over time, the number of uses expanded, said Whitehurst. “We use it on metal coping joints instead of caulking,” she said. “Caulk will break down over time. This was developed for marine applications, and it stands up to water very well.”
Although a primer isn’t always necessary when using EternaBond, RSI crews use the EternaBond primer in all cases. “At RSI Roofing we like to go above and beyond,” said Whitehurst. “We clean it and prime it so there’s no room for error.”
The company has found it to be the best solution for sealing edge metal on built-up roofs. “We just scrape it back, prime it with the EternaBond primer, and EternaBond it,” Susi said. “It’s just a faster repair that we used in the past, and we haven’t had any callbacks. It’s been performing quite well.”
At the La Jolla Village Professional Center, EternaBond was used throughout the complex to seal edge metal on an existing built-up roof. “The BUR was separating from the edge metal, and they were getting a lot of leak calls,” said Susi. “We cut it back to get a good bond, primed it with the EternaBond primer, and used the EternaBond tape. We used 2,700 feet of it.”
“Our sales guys use it when they take core samples of the roof,” Whitehurst said. “They put EternaBond over the hole while the test is being conducted, and then they put the core sample back and use EternaBond to re-seal it. I think every one of our guys carries it.”
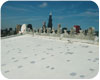
Eternabond was used to patch holes in the roof at the John G. Shedd Aquarium in Chicago before a soy oil polymer-based roofing system was applied. (Photo courtesy of EternaBond.)
Shedding Water at Shedd Aquarium
In 2004, the roof restoration and replacement project at the John G. Shedd Aquarium in Chicago was completed using the soy oil polymer-based Environmental Liquid Membrane System (ELMS) from Green Products. The existing roof was a patchwork of different systems installed over the years, including a 17-year-old modified bitumen roofing membrane over the facility’s Oceanarium and the 14-year-old Hypalon membrane over the west entrance of the facility.After using EternaBond to seal the leaks, the roofing contractor, Preservations Services Inc. of Romeoville, Ill., used solvent-free adhesives, HCFC polyisocyanurate insulation board, and granulated modified bitumen roofing membrane, which was coated with ELMS.
‘They were working on an icon,” said EternaBond’s Margarites. “Right on the lakefront, built for the Chicago Exposition in 1892, it’s got Hypalon, BUR, modifieds, EPDM, PVC, skylights. They could have torn it off and put on a new roof, but it would have been dicey with tropical fish and the exhibits below. They needed something that could work with all of these roof types, be a long-lasting solution, and be compatible with copings and flashings. They had to pick a system that would work with everything up there and that could be installed expeditiously. EternaBond was used at all of the seams on the metal roof, for cracks and seam splits in the Hypalon and PVC, and at brick parapets, copings, flashings and joints throughout. It was compatible with all of the existing roof types, as well as the soybean oil-based roof coating. They needed something the oil wouldn’t attack.”
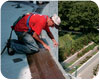
At the Shedd Aquarium project, EternaBond was used to repair roof leaks, as well as securing copings and flashings.
The Product
According to Margarites, the secret to the watertight roofing tape is its microsealant, which fuses at the molecular level. The product is based on technology originally developed for underwater/saltwater applications and adapted and reformulated for roofing. Margarites points out the product is environmentally stable and friendly, UV stable, has no off gassing, and performs at temperatures ranging from over 250 degrees Fahrenheit to 70 degrees below zero. The current formulation has been in use since 2000, with some 60 million linear installed.“We guarantee EternaBond for 10 years - any failure, we replace it, no questions asked,” he said. “We’ve replaced very little. It is expected to last for up to 35 years, so 10 years is a safe bet.”
Products include RoofSeal and a thicker version called RoofSeal Plus, both available in white, black, gray, tan, and with a 4 mil aluminum foil backing. A double-sided version called Double Stick is available, as well as fabric-backed version called WebSeal. Standard rolls are 50 feet long and 2, 4, 6, 8, 12, 18, 24, 36 and 48 inches wide. Custom lengths, custom widths (up to 48 inches), and custom slitting of the release liner are available so the product can be set up to best fit the application. It can even be rolled with the release liner on top to ease installation.