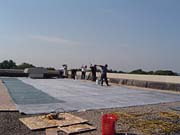
An upscale office building, 94 Dodge Place is on the main east-west corridor of West Omaha and houses a major producer of yellow pages and a prominent stockbroker. Its 38,160-square-foot roof includes a 4,000-square-foot upper penthouse roof over the mechanical room. A sloped, 4-foot-high EFIS-capped parapet surrounds the entire roof. The existing system was a gravel-faced four-ply built-up. Under this were two layers of urethane insulation on top of structurally sloped lightweight insulating concrete over steel decking.
Reroofing with EPDM was a possible option, but the building's maintenance engineer was concerned with the glycol coolant used by 11 large rooftop units. Though not likely, if a line burst during off hours of operation, the roof would be flooded with a solvent that could possibly compromise the membrane.
Boone studied available technical information on the effect of glycol on EPDM, which revealed that of the eight types tested, six had virtually no effect. Of two glycols rated "C," worst case, EPDM could experience a 0 to 50 percent volumetric swelling and a 0 to 60 percent loss of tensile strength in 30 days to one year. In short, the worst case scenario - a large spill with the most corrosive type of glycol at 100 percent concentration, with some ponding - would not "eat" or burn a hole in the EPDM. Any deterioration of the membrane would take an extended period of time. Damage could occur, but there would be time to repair or replace, if necessary.
With this point settled, Boone Brothers proposed four options for 94 Dodge Place:
1. Install a PVC roof in the quadrants of the roof occupied by the HVAC units.
2. Install a containment curb around the units.
3. Install a sacrificial sheet of EPDM around the units.
4. Install 90-mil EPDM around the units.
The building owner's budgeting considerations delayed the project till 2003. In the meantime, Boone Bros. also presented the client with the option of a 2001 Inc. wind-vented roof system. Its advantages are:
1. It could be installed over the existing roof, saving tear-off expense.
2. Using this system would reduce the number of fasteners needed to attach the substrate from approximately 18,000 for a mechanically attached system to 2,000.
3. Its self-drying capability would eliminate existing moisture in the substrate.
4. It comes with a 15-year warranty, upgradable to 30 years.
5. It has a proven track record of over 9,000 installations since 1979.
The building owner chose the 2001 system. In addition, with the savings generated from eliminating a tear-off and the extensive fastening requirements, 94 Dodge Place had more money available to increase the thickness of the EPDM membrane - from 60 mils to 90 mils. The increased thickness addressed concerns about any possible glycol leak. Additionally, the increased puncture resistance of 90-mil vs. 60-mil EPDM (almost double) alleviated worries over punctures from window washing equipment and ongoing maintenance activities.
Work commenced on August 15, 2003, and was completed on October 19, 2003. A small, experienced crew of five did the entire job from start to finish. There were no trucks or tar kettles on site after the roof was stocked. The only evidence of activity during those weeks of installation was the coming and going of the roofers who used the stairwell roof access. The roof was left watertight each evening before shutdown.
The 2001 system called for 7/16-inch OSB board around the perimeters, at all curbs and protrusions, and along both sides of all expansion joints. Because the height of the roof exceeded 30 feet, it was necessary for the crew to install 48-inch-wide OSB board along the perimeters, mechanically fastened at the rate of 12 per sheet. All other protrusions were surrounded by 24-inch-wide OSB.
Installing air seal rope between the new OSB board and the old roof created an airtight seal. The new EPDM is fully adhered to the OSB providing a strong perimeter attachment. Next, the crew installed a 5/16-inch-thick polyester mat - resembling carpet underlayment in appearance - over the gravel out in the field of the roof to provide protection to the EPDM.
The crew then put down the EPDM in 10-foot-wide strips up to 100 feet in length. Lap seams were spliced with 4-inch-wide seam tape in primed EPDM. By providing a uniform factory adhesive thickness and a peel-off backing, seam tape eliminates most wind-borne contaminates.
Finally, the crew placed 48 of the 2001 system equalizer valves in the corners of the roof and along the perimeter. The 2001 Co. specifies exact placement of the valves on each project. These valves take advantage of the vortex created by wind striking the windward side of a building. Wind-generated vacuum pressure pulls air out of the roof system through the valves. The harder the wind blows, the tighter the membrane is pulled against the substrate. A gentle breeze causes the EPDM to ripple slightly but as the wind increases up to about 15 mph or more, the membrane pulls flatter and tighter. 2001 Co. offers extended warranties covering winds up to 150 miles per hour.
An additional reaction occurs when hot air migrates from inside the building through nail and screw holes, deck joints and penetration gaps into the roof assembly. Low pressure causes liquid moisture in the roof assembly to change to water vapor. The water vapor is sucked out of the roof assembly through the valves. This causes the eventual drying of the substrates. This technology retards common roof moisture problems such as mold, blisters and deterioration of seams, flashings, fasteners and decks. Drying out insulation can return its "R-value."
For Jones, future maintenance on 94 Dodge Place will be fairly simple. A smooth-surface roof (as opposed to a rock ballast system) makes punctures much easier to find and repair, though the thickness of 90-mil EPDM will make the roof relatively puncture-free. Walk-pads were added to provide added protection from foot traffic to and from the rooftop units.
With long-term experience in the Midwest, Boone Brothers Roofing business strategy is to develop ongoing, long-term relationships with customers to provide service after the sale. 94 Dodge Place is another in a long line of successful roof projects.
Report Abusive Comment