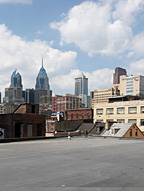
Within the United States, cold-applied systems entered the market in the 1960s, providing an alternative to conventional built-up technology. The appeal of the product's technology was centered on both its composition and its handling characteristics. The composition of the cold-applied mastic product most commonly included asphalt and solvent. Installers were able to apply the product with a brush, squeegee or spray equipment. This opened up new applications that would previously have been impossible with a conventional asphaltic system.
Rooftop Accessibility: In some cases, the usage of asphaltic products was precluded by difficult access to the roof, building height or the inability to locate kettles on the site. Cold-applied roofing products eliminate the need for kettles at the job site since the mastic can be brought to the roof in pails.
Liability Issues: Roofing contractors have increasingly gravitated toward cold-applied technologies to reduce their exposure to liability related to the use of kettles for built-up systems and torches for modified bitumen systems. With premiums on the rise, contractors can cut liability by avoiding the risks to workers associated with the use of kettles to heat asphalt as well as the fumes that can affect building occupants and workers. Torches used for the application of modified bitumen systems also represent a threat due to the potential risk of fires if not used properly.
Cold-applied Limitations
As usage of today's cold-applied asphaltic systems continues to grow, contractors have discovered the need to master the technology to avoid common installation mistakes. The product's benefits can only be obtained if good roofing practices are maintained at all times. To ensure a proper installation, it is essential that the cold-applied products are put down in dry conditions to avoid problems related to entrapped or ponded moisture. Moisture can destroy the bond by creating vapor pressure within the system, or prevent adhesion to the substrate.Contractors must also strictly follow application rate guidelines to avoid under or over application of the adhesive. A light application of adhesive threatens the system with weak bond strength. If too heavy, the system is at risk due to slippage between the plies. Roof systems applied with too much adhesive are susceptible to damage until the roof mastic cures.
Cold-applied systems require that the roofing plies be set in the adhesive properly to ensure system performance. Installers must be trained to properly handle roofing plies to make certain that the plies are adequately saturated and adhered to the insulation or existing substrate. Failure to do so jeopardizes the attachment and adhesion of the roofing system.
Next-generation Hybrids Emerge
As the appeal of cold-applied technology expands, new technologies have emerged that should permit dramatic new growth in the niche. Highly flexible asphalt-based polyether cold-applied adhesives provide the same handling characteristics as traditional cold-applied adhesives but with no VOCs making the products ideal for projects requiring the elimination of all fumes. The products are designed to be ready for immediate application without the need for stirring. Slippage concerns are virtually eliminated since the cold-applied adhesive provides a quick cure.Installation methods differ with this new variation from squeegees for smaller projects to spreaders for jobs requiring increased productivity. The product can be applied with an adhesive spreader that lays a 40-inch-wide path of product. Backrolling of the cold-applied adhesive is necessary to ensure consistent coverage.
This next generation of cold-applied adhesive is designed to perform with newly engineered single-ply cap sheets. EPDM and TPO membranes incorporating special fleece backing permit the cold process to penetrate, providing adhesion without contacting the membrane. These single-ply membranes are designed to provide excellent long-term performance since they are highly resistant to UV rays and the ozone.
With widths up to 12 feet, these cap sheets offer substantial improvements in productivity over conventional modified bitumen sheets with a width of 3 feet. System performance is substantially improved by this significant reduction in the number of seams.
The fleece backing on the membranes gives substantial support and strength to the system by providing puncture and tear resistance unmatched by a conventional modified bitumen or single-ply system. The warranty coverage for such systems can include coverage against damage from hail up to 2 inches. Additionally, the system puncture resistance permits the provision of a unique puncture warranty that provides added assurance for systems that receive regular maintenance traffic.
Roofing technology will inevitably continue to evolve to provide improved performance and installation characteristics. Cold-applied systems may finally have reached critical mass with the creative combination of cold-applied technology and the latest in single-ply technology. The resulting system provides a high-performance retrofit solution for existing smooth built-up roof or modified bitumen systems.
Report Abusive Comment