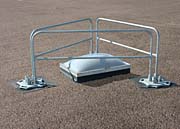
OSHA regulates roof skylight safety by means of both Part 1910 (General Industry) as well as Part 1926 (Construction). A majority of roofing firms who perform small repairs and miscellaneous replacements on skylight roofs are especially hard hit by these regulations. Their rooftop exposure for a 10-square repair may be limited to a day or two and their material/labor/equipment budgets are usually very tight. These are generally the roofers with the highest skylight hazard exposures and skylight fall accident rates, because there are few practical, affordable TEMPORARY skylight protection systems for pitched or flat roofs available on the market today. Sometimes a larger contractor hired to completely replace a 300-square warehouse roof may have the ability to bid his project scope to include compliant and adequate skylight protection.
In some large projects today, especially on roofs that are flat or below an 11-degree pitch, a permanent guardrail system or rigid screening is designed into the plans and specifications. These devices permit the worker making roof access years later to be protected by the same guards or guardrails which were originally installed. The predominance of skylight fatal falls occur on roofs where there was no permanent guarding device initially installed by the property owner and where there is no provision in subsequent repair contracts to install either permanent or temporary OSHA-compliant protective devices.
Years later, along comes a roofing contractor faced with competitively bidding a roof repair or replacement. The property owner may have little need to specify and pay for either permanent or temporary skylight guarding which would significantly increase the total lump sum of the bid. The contractor is clearly mandated by OSHA with the "duty" to protect his employees from falls through skylights (and off edges) where the height exceeds 6 feet above a lower level.
A Market Full of Skylights
Skylights fall into many operational categories, material groups, structural shapes and design styles. As long as the panel or glazing is below 42 inches above the deck, they are considered potential fall hazards for a roofer to work around or near.The problem inevitably becomes all the more insurmountable when the owner of the roof declines to pay anything extra for the cost of installing these protective devices. Just what does OSHA expect a roofing contractor to do? Answer: Protect his workers from skylight falls regardless of cost or schedule.
We should review several of the skylight protection methods available to the roofing contractor before he accesses the roof: 1) Which ones comply with OSHA's skylight standard? 2) Which ones are practical to build and feasible to work around? 3) Which ones do not create a greater hazard than the one that is being abated? 4) Which ones are affordable?
Warning Lines, Controlled Access Zones and Safety Monitors
Warning lines (1926.502(f)), controlled access zones (1926.502(g)) and safety monitoring 91926.502(h) are methods that OSHA standards PROHIBIT around skylights. According to the compliance officers I spoke with in Region I and II, the only exemption from this prohibition would be if the skylights happen to be within an established leading-edge controlled-access zone. Otherwise, the skylight opening or finished unit must be guarded by screen, cover or guardrail before the controlled-access zone is moved ahead with the leading edge exposing the skylight.Screening or Covering Skylights
OSHA Standard 29 CFR, 1910.23(a)(4) states that every skylight "shall be guarded by a standard skylight screen or a fixed standard railing on all exposed sides. The requirements for these skylight screens are called out in 1910.23(e)(8):"Skylight screens shall be of such construction and mounting that they are capable of withstanding a load of at least 200 pounds applied perpendicularly at any one area on the screen. They shall also be of such construction and mounting that under ordinary loads or impacts, they will not deflect downward sufficiently to break the glass below them. The construction shall be of grillwork with openings not more than 4 inches long or of slatwork with openings not more than 2 inches wide with length unrestricted."
Covering the skylight with either site-built or pre-manufactured screens can be problematic for the roofer who is just "passing through" and has not pre-planned his project carefully. If the corrugated aluminum, galvanized or galvalume roof deck has one or more integral, flush-mounted translucent fiberglass panels, even applying a temporary 5/8-inch CDX plywood cover can pose some serious tactical problems. If the fiberglass panel is over 8 feet in length or 4 feet in width, one 4-foot by 8-foot plywood sheet by itself will not sufficiently protect the worker.
OSHA considers any opening or potential opening in a floor, roof or walking/working surface greater than 2 inches in its least dimension to be a "hole." If it sufficiently covers the fiberglass, how can it be securely fastened to prevent accidental removal and still withstand the minimum 200 pounds dead weight without deflecting or damaging the skylight material? If it is wider or longer than the ply score, a framework of 2-inch stock or light-gauge metal studs screwed with neoprene washers through the roof panels into the purlins below may provide the temporary support for the plywood sheathing over flush skylights.
There are the labor and material expenses in construction of any temporary skylight covers. During demobilization there will undoubtedly be subsequent waterproof repair of holes generated during installation. Whether one or 100 skylights are encountered, the manufacturer's warranty of the roof materials may also be called into question.
A 10:12 pitched corrugated galvalume roof with 30-inch-wide by 12-feet-long flush fiberglass skylight panels may pose another difficult protection situation not easily solved without some type of screen or solid cover. I have installed 1 1/2- by 3 1/2-inch galvanized C-channels tech screwed over the ribs on either side of fiberglass panels and spanned them with 4-foot by 8-foot 5/8-inch CDX sheets, lapped in the middle. These were clearly spray stenciled: "Danger! Skylight Below, Do Not Remove." These were screwed down 6 inches on center into the galvanized channels with washer-head self-tapping sheet-metal screws.
While we could safely stand two well-fed roofers mid-span and not damage the skylights, it took the better part of a shift to securely cover just a dozen skylights. Subsequent removal also required patching the screw holes created by the mounting channels. In another case, on a very steep 14:12 aluminum panel roof, the last phase of the repair operation was to remove each skylight cover and re-coat the fiberglass surface with a UV-resistant, acrylic-resin. From initial access until final egress on the 78-degree sloped roof, we were protected by a personal fall-arrest system (PFAS).
Most standing-seam roofers are aware that the skylights they encounter are curbed to some degree and may offer a mounting surface to attach any number of pre-manufactured skylight screening devices. There are several manufacturers of versatile metal screen systems, which are designed to cover these and other types of skylights.
For those rare occasion where standing-seam roofs incorporate flush-mounted translucent skylight panels, there are several manufacturers with anchor devices that set-screw and clamp onto many variations of the standing-seam pattern. From these anchor points, heavy-gauge steel screens are fastened down using integral screws. When the roof pitch is over 4:12, then the installation of such clamp and screen devices must be performed while using PFAS to another suitable anchor point. I have often heard it reported that a worker initially protected by PFAS ultimately fell to his death as his nylon lanyard was severed during the penetration of the skylight. Although sometimes cumbersome, the use of 6-foot by 1/4-inch aircraft cable lanyards is strongly advised when working around skylights to prevent such accidents.
Guardrail Skylights
The construction standard (1926.500(b)(4)) clarifies skylight hazards encountered during construction, alteration, renovation or repair phase as follows: "Wherever there is a danger of falling through a skylight opening, it shall be guarded by a fixed standard railing on all exposed sides or a cover capable of sustaining the weight of a 200-pound person."Ideally, this guard system should be able to withstand this 200-pound person falling from a height of 4 feet. If it were a guardrail system it would have a 200-pound-resistant top-rail at 42 inches vertically, 150-pound-resistant mid-rail (21 inches) and a 50-pound resistant nominal 4-inch toe-board. The guardrail components should be able to resist these loads applied to the mid span of the guardrails in an outward or downward vector without structural failure or compromise.
If a 42-inch-high guardrail system is installed perpendicular to the plane of the steep roof deck, its effective height would be below minimum height required. In order to be compliant, the guardrail would have to be either 42 inches high vertically or several inches higher when measured perpendicularly to the roof plane.
Roofs with installed skylights can be either flat, low slope or steep pitch. While an OSHA-compliant guardrail system is meant to withstand a 200-pound mid-span load on the top rail and 150 pounds on the midrail, this is based on a primarily level working surface. Should a roofer slide or even tumble into a guardrail system, his/her impact mass may be many times greater than the minimum resistant strength of the guardrail. Any structural failure would present the same hazard as an unprotected fall with the additional force of the guardrail impact. The roofs supporting them can be asphalt composite shingles, corrugated or standing-seam metal, flat built-up asphalt, and stone ballast or elastomeric membrane.
For the contractor who is about to send his workers onto a roof deck in which skylights already exist, the problem arises how to construct and install temporary physical guarding that is OSHA-compliant (and thereby structurally resistant to fall impacts) and yet is fairly simple in design and inexpensive to build. That sounds about as reasonable as a "day-stretcher."
If the scope of work is simply to "stitch" down a low-pitch metal roof, replace any stripped-out fasteners, remove and replace a few corroded panels and recaulk and waterproof the roof penetrations and flashing, then a temporary guardrail system could be considered suitable. A 42-inch-high, four-corner guardrail system built from 2-foot by 4-foot #2 hemfir designed with a figure-4 base design may be considered adequate protection. I would add diagonal bracing along each side of the rectangular guardrail to help withstand any physical impact from the "uphill" side.
If the uprights are perpendicular to the pitch of the roof, they must then extend even further and be at least 42 inches high measured on the vertical plumb line from the top rail. If they are built plumb, then 42 inches is sufficient. I have constructed these clumsy apparatuses before and anchored them on top of the ribs by building up a shim pack beneath the 2-foot by 4-foot base plate and screwing it into the purlins with self-tapping #10 tech screws through a bed of GE silicone seal.
We would then install two screws in each flat valley across the top of the system and several in the top end of each of the pitched base plates. Several screws into the purlin below the skylight were sufficient to withstand any side impacts the guardrail might suffer. I would test them for strength by physically "hip-checking" into them while safely tied off in a PFAS. After removal we filled the holes with an oversized gasket screw coated with phenolic resin (®Geocel).
If a flat roof required stripping out and multi-layered mopped asphalt and stone ballast, then the skylight guardrail system would obviously become at least a nuisance and at most a major impediment to completing the demolition and new work. The use of PFAS can also be frustrating, as the lanyards, lifelines, retractables and hardware were continually being fouled by the asphalt and would eventually become inoperable. A system of skylight screens or guards are much more suitable for these conditions.
Cal-OSHA Skylight Guarding
In August 2003, California's OSH Standards Board began a series of public hearings to consider revisions to Title 8 of the Construction Safety Orders, California Code of Regulations. Its purpose was to review the existing skylight guarding regulations for inadequacies and failures to protect rooftop workers. As Cal-OSHA State Plan standards are much more strict than the federal OSHA, they often become precursors to federal OSHA standard revisions. Therefore we can expect this trend to lead to new safety requirements concerning skylight protection. Its proposed revisions include: 1. Installation of temporary guardrails or covers for skylights shall be "designed by a Qualified Person." 2. Minimum skylight cover strength "shall be 400 pounds (not 200) or twice the weight of the employees, equipment and materials that may be imposed on any 1-square-foot area of the cover at any one time. 3. An employee approaching within 6 feet of any skylight shall be protected from falling through the skylight or skylight opening by any one of the following methods: A. Skylight screens B. Guardrails C. Personal fall protection system D. Skylight covers E. Temporary warning lines (roofs under 4:12 pitch) F. Qualified Persons within 6 feet proximity of skylight with safety monitor when any other method is infeasible or creates a greater hazard (roofs under 4:12 pitch).Conclusion
The manufactures of skylight guardrail and screen systems I spoke with while researching this article have business plans that only address permanent installation. As a matter of fact, several of them have gone so far as to discourage contractors who need to tackle the temporary skylight guard issue from buying their product. They do not want the obvious and serious liability that would result if their product were used for any purpose other than that for which it was designed: permanently fastened skylight guarding installations.As soon as a contractor modifies any safety device either from its original function, installation instructions or physical configuration, OSHA will cite him for "field modifications" without maintaining a site-copy of the written consent of the manufacturer for such changes. On the other hand, the major manufacturers I consulted were not interested in going after this temporary skylight guard market for various and well-founded reasons: The cost of R&D; stringent and expensive testing laboratory approval protocols; a costly series of design prototypes; as well as a gigantic minefield of legal liability that may arise. As one CEO eloquently put it: "Why would I want to pay a lot for that much trouble?"
After a hundred hours of research on this subject I can only conclude, that it's ultimately up to the roofing contractor to temporarily protect his workers from falling through skylights. He must invent and build sufficient protection regardless of the type and pitch of the roof, the money he put in the budget; and the time he has to get the job done. No one currently in the manufacturing field is looking for practical ways to solve his temporary skylight protection problems. He can't even legally modify an existing skylight guardrail or screen to fit into his temporary solution. On the other hand, everyone is ready to sue him for injuries, raise his insurance rates, send him into an assigned-risk pool, or cite him for non-compliant safety procedures.
The OSHA standards clarify the contractor's duty, no matter the means, cost or time required, to prevent his workers from falling through an exposed skylight. And just like most safety compliance issues, temporary skylight protection is primarily about the "non-event." As one contractor who I have known for years confided to me, "I only guess that I've been successful after nothing bad happens. And even then I'm not sure."
Note to RC readers: If you have discovered a successful solution to your on-the-job temporary skylight guarding problems and feel like sharing them with others in your trade, feel free to e-mail me with your technical solutions. Be as detailed as you can and I will collect them, give you credits and discuss them in a future Roofing Contractor article.
Report Abusive Comment