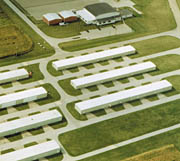
In addition, the benefits of a comprehensive maintenance approach go beyond initial economics and stopping rust or leaks. The maintenance procedure can also deaden sounds from rain and hail; cool the building; and make it more energy efficient by reducing air-conditioning demands. The cooling of the roof surface adds an often hidden feature: It reduces thermal movement and the cycle that normally develops into additional maintenance costs.
Developing market awareness of available options is the key to assisting building owners in making the right decision. For years, owners and some contractors have had the maintenance man attempt to stop leaks with common plastic roof cements. After a few short freeze-thaw cycles, what was considered an economical solution at the time soon fails. The process is repeated over and over again. The development of new problems may not yet have progressed into leaks, but fasteners are already in the process of losing their seals, rusting, and pulling out. Building owners and many contractors are simply waiting for the inevitable replacement.
This process continues to result in many property owners deferring appropriate maintenance until it is too late. Greater savings occur when problems are not ignored to the point that replacement becomes the only option. Before reaching this point, building owners and facility managers must decide what steps to take to solve common metal-roof maintenance problems, preventing the need for premature replacement.
On the other hand, many owners feel that tearing off an old roof and replacing it will be the end of their problems. Consider these issues: A complete new roof usually has a construction warranty only (nothing covering leaks), costs about three times more than a roof restoration, and has to be amortized over 39 years of the expected roof life. Down time is also a factor while overhead cranes remove panels. Stopping leaks and corrosion can be done more economically with a warranty covering the building owner’s needs. For these reasons alone, many are turning to more thorough maintenance. They see the payback of quality roof restoration, with the lowest costs over the life of the warranty and immediate deductibility.
Advanced technology has resulted in the formulation of elastomeric coatings that provide long-term solutions for metal roof problems. Finding ones that employ a systematic approach, coupling traditional materials with products to enhance the metal roof condition and prevent problems, is essential for greatest dependability. To simply overcoat a metal roof or take pot shots at repairs is one thing. To address each component as part of the process and dependably prevent problems is another. Putting it all together in a simple and comprehensive approach is what ultimately provides long-term value.
This is why it is not unusual for contractors to work in conjunction with various resources. Disciplines working together can solve roofing problems economically and efficiently. This holistic approach is grabbing the attention of metal roof contractors who were once content with only new construction. As a result, they are now able to offer more cost-effective options.
It is important for the contractor to pick a manufacturer that will offer support and is quick to find a solution to the problem without worrying about who is responsible or who is to blame. More often than not, there is usually a simple solution when a problem occurs. However, the first and foremost concern is to satisfy the customer. No amount of effort can equal the power of a testimonial from one satisfied end user.
Contractors need to work with manufacturers who are willing to walk away from roofs for which maintenance procedures are not appropriate rather than risk the reputation of both parties involved. Building owners need to know manufacturers have specific written guidelines covering installation.
With so many coatings and roofing systems on the market, it’s hard to decide which one is best for the applicator and the owner. Manufacturers can help with this. An integral part of the manufacturer’s quality assurance program is a certification program for contractors. The certification program trains contractors to the standards of the manufacturer’s application procedures. The program provides the contractor with the confidence he needs to successfully accommodate customer needs. It provides him/her with all the advertising, sales tools, product specifications and technical support needed to turn a building owner to a signed contract, and complete the project skillfully.
The follow-up is just as important. The manufacturer should also require yearly inspections to identify any problem areas that need attention before they lead to costly leaks or permanent damage. Preventive maintenance is realistic; expecting no possibility of damage from workmen traffic or acts of God, is not.
The process of restoring a metal roof should always start with a complete and thorough examination of the entire roof surface. Facilities managers and/or maintenance staff should be consulted for past problem areas on the roof. Insulation and the underside of the roof should be checked for possible wet insulation or condensation problems. Condensation is a major cause for callbacks due to lack of proper ventilation. Fasteners must be inspected to determine if they are loose or stripped. They should be tightened to torque or replaced with a larger fastener. Extra fasteners should be added to areas where gaps are present, especially at end laps.
After the roof is repaired mechanically, the restoration begins. All rust must be treated according to the coatings manufacturer and power washed to obtain a clean, dry surface. Seams and fasteners should get specific attention — use systems that reinforce them with compounds that provide enough tensile strength and elongation to move with the roof’s normal constant expansion and contraction.
Penetrations such as HVAC units, stacks, vents, etc., should be similarly reinforced. Before the first application of the field coat, the entire roof should be walked and additional repair material applied to areas that need attention. After the entire project is complete, the building owner is left with an attractive roof that is leak-free, seamless, quieter and which can be expected to outperform any of the repair procedures mentioned above when performed alone.
Maintenance programs are needed on all roofs. When performed in time, they are always more cost effective. All roofs should be walked at least once a year and checked for clogged drains, gutters and downspouts, as well as the effects of time and weather. Penetrations, seams and fasteners should be checked and any damages corrected. A preventative maintenance program provides a positive economic benefit, as well as peace of mind for the building owner. It will extend the life of their metal roof far longer than if left ignored. It is one great example where a stitch in time saves nine!
Report Abusive Comment