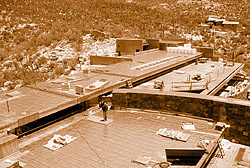
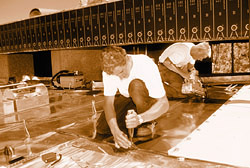
What is perhaps most unusual, though, is that the specs call for a 28-gauge (0.4 mm) stainless steel roof. “The owner wants a place for family gatherings, and a roof that will last through generations,” explains project designer Les Wallach, founder of Line and Space Construction LLC, architects for the project as well as general contractor. The firm’s chief focus is on institutional projects such as the National Historic Trailscenter in Casper, Wyo., or the Arizona Sonora Desert Museum Gallery and Restaurant complex near Tucson. “This is our eighth or ninth residence, but it's much larger than the others, which ran from 3,000 to 6,000 square feet,” Wallach explains.
The home is situated on 10 acres of ground so rugged that even the tennis court required extensive blasting. While others may view the project as complex, Wallach points out that the roof is relatively simple. “I read about welded stainless steel roofing in a European magazine and showed it to the owner. He got excited about the technology and agreed that stainless would be ideal for his home. There was a lot of legwork, though, to get the German contractor here with his crew, equipment and materials.”
The contractor, Architectural Stainless Service Center (ASSC) of Germany, points out that they were unable to source the materials in the United States, so they had to bring it all with them. “We do projects in all the countries that surround Germany,” explains Klaus Maier, managing director. “This is the most distant project we’ve taken on. The challenge was to make sure to have everything we needed at the start so we wouldn’t have to wait three weeks for something to be shipped from Germany to Arizona.” He notes that the list of materials included rolls of stainless roofing and closed-cell membrane, as well as the necessary machines and hand tools. It took three days to get the materials and the crew through customs.
The technology is rather simple. ASSC workers cut lengths of 625 mm (about 24 inches) wide, 0.04 mm thick (28-gauge) of 316L stainless, then bend the edges 1 1/4 of an inch to form a seam. After folding, the seam stands 3/4 of an inch high, and then is welded in a process that more resembles ironing than welding due to the low incidence of sparking and the size of the device.
During repair work on another stainless roof, the Chrysler Building in New York City, Maier investigated and found, “That building is 68 years old, but there is no corrosion, no loss of thickness in the stainless. There have been problems with folded seams coming apart over the years. That is why we weld all the folded seams on our projects. Further, we’re using 316L, or low-carbon stainless, which is even more stable than the grade 302 used on the Chrysler Building. Further, the expected life of 180 years or so is far above a typical built-up flat roof where the pitch is just a 1/4 inch per running foot.” This house measures 240 feet on one of the longer levels, with the roof at that level standing 40 feet above the desert floor.
Striving to honor the owner’s request for as low a profile as possible on this high- profile project, the architect did not reveal the cost of the structure, just as Maier declined to mention the value of his roofing contract. Maier did note that the technology is three to four times more expensive than that of built-up roofing.
But with 10 times the life expectancy, one can see that, in the long run, welded, low-carbon stainless steel is the most cost-effective route to go. “The cost of maintaining a traditional built-up roof easily overtakes any initial savings,” Maier emphasizes.
He notes that two different finishes of stainless are being used. “We have the highly reflective mill finish on the flat roof planes, while sharkskin forms the building’s fascias.” The sharkskin bead or sandblasted finish isn’t reflective, which keeps the building from casting reflected light into neighboring homes. It also provides a handsome maintenance-free permanent gray tone that looks good against the generally intense blue sky.
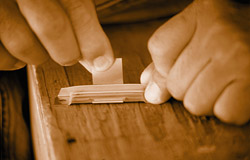
Prepping the Roof
Traditional joists and beams support the structure, but a layer of 5/8 plywood provides a solid surface for the thin-gauge stainless. ASSC’s crew of three then covers the plywood with 3/16-inch-thick closed-cell packing foam. Lengths of folded stainless are then placed atop the foam, at a right angle to the foam. The foam is not stapled, but immediately covered with metal. “Our crew can finish about 150 square meters a week,” Maier continues.
Bob Clements, who is both the project architect and job-site supervisor, then speaks up, “Chimneys, skylights and plumbing account for 90 to 100 roof penetrations to work around.” Maier points out, “Basically, we are able to work at just 66 percent efficiency because of the time it takes to properly deal with those penetrations.”
Climate Factors
Summer desert heat is also a challenge. “We have had problems with the welders because of temperatures. Yet letting a welder rest is a slow, slow way to cool it enough to resume operation. That’s why we use a chiller to help keep our welders cool and working.”Another factor is heat build-up by the roofing itself. “That’s why it’s highly reflective. Then heat increases just 30 percent or so, rather than double the ambient temperature,” Maier continues. (Sunglasses are part of the working uniform.) “Our system also includes sliding cleats fastened to the plywood that allow for thermal expansion and prevent the roof from bubbling on particularly hot days, yet keep the seams themselves from moving. This material can move 1.6 mm per meter per 100-degree centigrade temperature change.”
A homogenous steel roof al-so becomes a catcher for lightning, so lightning protection is part of the system. “We’ve installed a dozen ground connectors. We’re using the deck as a conductor itself, so there is no maintenance required for lightning protection.” The soundness of the water barrier is thoroughly tested. Helium is injected under the stainless and then a helium sniffer is used along seams and intersections to search for leaks. A few spot welds at detected leaks are all that usually is needed to seal any problem areas.
Learning Curve
Maier, who came to metal roofing just seven years ago after a generation in oil exploration, admits one of the features he enjoys with this system is the shortness of the learning curve. “After 14 days under supervision in a shop setting, a new employee who already has experience with other metal roofing systems can install this system correctly and safely. Safety is important because this gauge is so thin that cuts are more of a danger than with other roofing materials. They also learn that this metal is unforgiving when it comes to incorrect measurements. You have to avoid re-bending because each time you bend stainless you have more local hardness to overcome and that lengthens the lay-down time considerably. Eventually the seams get brittle, and reworked seams can split.”He then noted that the first thing newcomers learn is to never mix carbon and stainless steel. “Carbon will corrode on stainless. If you mix the two steels, you’re implanting corrosion, and moisture migration will become a real problem.” Maier concludes: “Laying stainless is 16 percent slower than laying other metal roofing systems. But when it comes to maintenance and expected life span, stainless is unbeatable.”