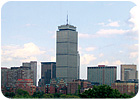
Built in 1964, the 52-story Prudential Tower in Boston is home to hundreds of tenants. Fondly called “the Pru” by locals, it offers a 360-degree panoramic view observation deck, a shopping mall and one of Boston’s Premier restaurants, Top of the Hub, on its highest floor.
As it approached its 40th birthday, the original coal tar roof was starting to show its age. The building owners, concerned about their long-term investment, commissioned a study. Roofing consultant Facility Engineering Associates (FEA), PC, of Virginia and their senior project manger Jim Justus were asked to determine if the evidence of water leaks meant that the best course of action would be a total roof replacement. After careful study in 2003, the engineers at FEA came to that conclusion. They recommended that all three original roof areas - the 51st floor, the 54th floor and the 55th floor roofs - be replaced.
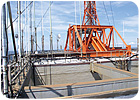
The 50-plus antenna mounts on Boston’s Prudential Building created numerous challenges for the installation crew.
Designs were completed and construction started in early 2004. The now 40-year old-roof would present a host of challenges. The 51st floor featured an inverted roof with a concrete slab over the roofing membrane. It also included the window washing rig rails and selected mechanical equipment. The concrete slab would have to be removed prior to removal of the membrane, and the roof would have to remain watertight. The 54th floor has over 50 antennae mounts, three electrical equipment boxes, and many other pieces of equipment. The cooling towers are also located in recessed areas on the western side, and they operate year round. The 55th floor has the main mast antennas, a service elevator penthouse, and numerous other additional antennae mounts and pieces of equipment.
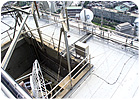
The crew needed to be ever vigilant of the microwave and radio wave energies flowing from the countless transmission sources, as transmission could not be interrupted during the project.
To accommodate the restaurant and the building’s other high-end tenants, much of the work would be done at night (after the dinner hour and before the breakfast service). The old roof on the 51st floor, placed under a concrete slab, would require noisy demolition saw cuts and a constant flow of wheelbarrows on elevators to take the over 200 cubic yards of concrete down to street level for disposal.
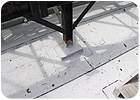
Soprema’s Alsan flashing was used on the hundreds of roof penetrations.
The application skill of Titan combined with Soprema’s system designed for the dramatic wind uplift at 55 stories, proved the winner. Additionally, the challenge of flashing literally hundreds of penetrations was easily met by using Soprema’s Alsan Flashing. The proprietary material saved labor and installation time. Alsan flashing was simply painted on. The field base sheet was Sopralene 180 sanded and the field cap sheet was Sopralene 250 FR GR.
“With Soprema, we knew we were assured of experience, quality and a solid reputation,” stated Jim Justus. “Soprema’s multi-ply system provided superior puncture and tear resistance, and their past history indicated the products would exceed the owner’s requirements. The key to Soprema’s system for FEA was the granulated cap sheet, which protects the membrane from puncture, and the Alsan flashing compound, which dramatically eased the constructability of the flashings. Those two items were critical to selecting the system.”
Report Abusive Comment