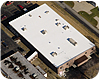
When Allen Aircraft Products Inc. of Ravenna,
Ohio, built a 25,000-square-foot stand-alone building to house the Aircraft
division’s assembly and test functions, they chose a TPO system from Mule-Hide
Products Co. for the roof.
For more than 60 years, Allen Aircraft Products Inc. of Ravenna, Ohio, has grown right along with America’s aerospace industry. From the B-50 bomber to the Boeing 777, the northeastern Ohio company has supplied virtually every American commercial, military and private aircraft with fluid system products. Its Metal Finishing division provides coatings for the Space Shuttle and other NASA and military programs.
When planning its most recent expansion - a 25,000-square-foot stand-alone building to house the Aircraft division’s assembly and test functions - the team at Allen sought a roofing system that would not only stand up to the area’s snowy winters and gusty falls, but also help reduce cooling costs during the summers, when temperatures can soar into the 90s.
A TPO (thermoplastic polyolefin) system from Mule-Hide Products Co. Inc. fit the bill on all fronts - so well, in fact, that a similar system was used earlier this spring to replace the 3,000-square-foot roof over the firm’s administrative offices. A 0.060-inch-thick white TPO membrane was used for both projects. On the new building, the membrane was mechanically adhered to the roof deck. A fully adhered system was used in the reroofing project. In both cases, 12-foot wide by 100-foot long sheets were used.
“Weatherability, durability, energy efficiency and, of course, cost, were our key considerations,” said Kevin Barbeck, Allen’s engineering manager. “The strength of the heat-welded seams and the white color, with its ability to help us reduce cooling costs, were the deciding factors in choosing the TPO system.”
Contractor Boak & Sons Inc. of Youngstown, Ohio, completed both projects. Founded in 1974, the firm specializes in commercial and residential roofing, commercial and residential insulation, and residential siding and windows. The firm was originally established as an insulation contractor, but rising energy prices in the 1970s led founder Sam Boak to expand into roofing so he could offer area businesses and homeowners the latest energy-saving products and techniques. Continued diversification of product offering included the addition of single-ply commercial roofing to the firm’s arsenal. TPO was added to that lineup approximately three years ago.
Quick, Easy Installation Helped Reduce Costs
Wide membrane sheets, a robotic welder and a little assistance from Mother Nature allowed crews to finish the projects on schedule and helped reduce costs.
It took an eight-person crew just one week to install the 22 membrane sheets on the new building. Bob Fergus, project manager with Boak & Sons, estimates that it would have taken 20 percent longer to install an EPDM system and a full 50 percent longer to install a traditional built up system.
“The automatic heat welder can do the seams a lot quicker,” Fergus said. “It runs on its own, putting the appropriate amount of hot air on the seam and fusing the two sheets together.”
Frank Burk, sales representative with Mule-Hide, added, “With a TPO system, a robotic welder automatically does all of the seaming for you. You can finish a 60-foot seam in four minutes, rather than an hour.”
The reroofing project, from tear-off to completion, took a five-person crew just four days to finish. The use of 12-foot-wide sheets further sped up installation of both roofs by reducing the number of seams that had to be welded. While some manufacturers only offer 10-foot-wide sheets, Mule-Hide gives contractors a choice. The extra 2 feet likely shaved 15 percent from the time needed to complete the seaming, according to Burk.
Mother Nature cooperated, too. Rain didn’t keep the crews off the roof during either installation. Crews also didn’t have to contend with the mess and safety concerns associated with other roofing systems.
“TPO is much more crew-friendly,” Burk said. “You’re not working with torches and open flames, so you don’t have the fire risk. It’s also cleaner to install than asphalt. You don’t have the smell and don’t get all that black muck and goo jumping on you.”
Durability, Weatherability Were the Key
Allen’s top priorities in choosing a roofing system were, of course, weatherability and durability. “Our weather can be severe,” Allen’s Barbeck said. “Obviously we don’t get hurricane-force winds, but occasionally we may see gusts of 50 or 60 miles per hour. We haven’t had a lot of snow since the roofs were installed, but we’ve had heavy rains. The roofs have performed well. They’ve done exactly what they’re supposed to do.”
The TPO membrane is lightweight but highly resistant to tears, impact, punctures and wind uplift. It also is reinforced to accommodate the building’s thermal expansion and contraction and minimize shrinkage, ensuring watertight integrity.
The heat-welded seams provide additional strength, flexibility and wind resistance.
“The seams are actually stronger than the membrane itself because you’re fusing two layers into one homogeneous piece,” Boak & Sons’ Fergus explained.
Cool Roofs Ease Energy Costs
Skyrocketing energy costs and summer temperatures that frequently rise into the 90s also put energy efficiency at the top of Allen’s priority list.
“The membrane’s white color and the fact that its reflectivity and emissivity can help with our cooling costs were absolutely important factors,” Barbeck said. “Other systems we looked at were darker and wouldn’t have offered the same energy efficiency.”
Based on industry studies, Allen can expect that its cooling costs will be 10 percent to 30 percent lower than other options, and that its cooling equipment will last longer with less use.
On Allen Aircraft Products’ “to do” list of future projects is replacing the roof over the old assembly and test area. “It’s still a relatively new roof, but when the time comes, I imagine we’ll replace it with a Mule-Hide TPO system,” Barbeck said.