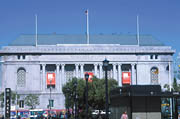
Of course the answer is B! Zinc is not for the faint of heart, but this “new” material has been used extensively in Europe for over a century, including 84 percent of the roofs in Paris. “Zinc is similar to copper in that it lasts a long time,” says Jonathan Lowy, technical marketing manager for Umicore Building Products USA Inc. Umicore’s headquarters are in Belgium and its building products division is located in Paris. The company introduced its product, VM Zinc, to the North American market about three years ago, though it has been producing zinc for about 170 years. “There are some 130-year-old zinc roofs in Europe. These may be exceptions, but zinc roofs will definitely last 50 to 80 years,” says Lowy.
The key is learning proper installation techniques. Umicore offers ProZinc training classes for installers at its headquarters in Raleigh, N.C., and at its West Coast site in Portland, Ore. The three-day sessions are conducted by master craftsmen. Onsite training is also available as is assistance once the job has begun. In addition, the company’s engineers will work with installers on shop drawings.
“The main difference in installing zinc is that all the flashings are folded, there are no ridges,” Lowy explains. “You use stainless steel clips. No other materials are used — no paint, varnish, coatings — thus, the material is low maintenance, which is key for the building owner.”
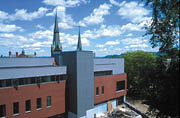
Fun Facts
Umicore’s product as a building material is actually an alloy: it is 99.995 percent pure zinc produced by an electrolytic process, alloyed with traces of copper and titanium added in controlled quantities.“Natural zinc is shiny and silver, but it darkens to gray,” Lowy explains. “We also make a preweathered zinc that is gray (Quartz-Zinc) or black (Anthra-Zinc). Anthra-Zinc is good to use with slate because it is almost the same color.”
According to literature published by Umicore, there are a few things to keep in mind when working with zinc:
Malleability: A distinct advantage of zinc is its malleability. The inherent softness of the material and its ductility allow it to be shaped into almost any form.
Cold weather installation: If the temperature of the zinc (not the air) is not at least 45 degrees F, it may be subject to brittle fracturing.
Thermal expansion: Zinc has a thermal expansion of 1/64 inch per foot for a temperature variation of 212 degrees F. To accommodate the change in length, sliding clips are used to hold the panels in place.
Imperfections: Zinc has a “self-healing” nature, so the formation of the patina will obscure any fingerprints, minor scratches and hard-to-remove dirt or grease over time.
Corrosion: In general, zinc is most vulnerable from its underside. To prevent corrosion, a well-ventilated airspace is required, along with a protective barrier.
Other metals: zinc can be used with aluminum, stainless steel and galvanized steel. It cannot be used with copper and non-galvanized steel.
Wood: When laying zinc on a wooden substrate, it can be used with pine, spruce, Scots pine and poplar. It is not compatible with larch, oak, chestnut, red cedar, Douglas fur and white cedar. It is also not recommended for use with plywood or OSB.
Other materials: Zinc cannot have direct contact with bituminous felt because of the risk that the felt may retain water and cause the zinc to corrode. Zinc also needs to be separated from concrete and reinforced concrete.
“Roofing contractors should know that VM Zinc supports them with training, drawings, etc.,” says Lowy. “Also, while zinc may be considered a ‘new’ material, it is actually tried and tested. It’s not a mystery material. “As long as you know how to install it, it’s fairly easy to use. Installers are nervous at first, but they are happy with the material once they try it. It’s easy to cut, fold and solder.”
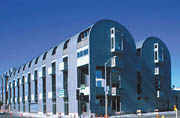
On the Front Line
So who are these brave contractors who have found success with zinc?Roof Technologies Inc., Harvey, La., is a commercial contractor that does about 40 percent metal. It has been involved with three different zinc jobs over the past year: a more-than-400-square parish courthouse, a small church, and the Freeman Business school at Tulane University in New Orleans.
Two workers were originally trained for zinc last year and now about a dozen others have worked with the material.
“Once you go through the training and get used to it, zinc is nice to work with,” says Sam Rabalais, project manager. “It handles and goes on like any high-end metal. You use European methods – no rivets, caulking, etc. I like it, I think it will be big for the high-end market.”
Mike Payton of Payton Sheet Metal in San Francisco agrees. “Zinc is very popular with architects. Price-wise, it’s about the same as copper. And it lasts like lead, but it’s not a hazardous material. Zinc is a perfect replacement for lead because of its color.”
Payton Sheet metal used 30,000-square-feet of VM Zinc for the roofing and siding on the Third Street Lofts, an apartment building in San Francisco. According to Payton, the biggest challenge on this job was not related to the material, but to the fact that the building has an eliptical layout. “It’s not a true radius, so we had to change the curves,” he explains. “But the zinc looks fantastic.”
Another challenging job was a 5,000-square-foot private residence with tapered panels. Payton Sheet Metal also did the roof on the new Asian Art Museum in San Francisco.
“It’s great working with zinc,” says Payton. “It’s not painted so it won’t peel, chip or chafe. It’s also easy to solder so it’s watertight, and not caulked like painted metals. The customer is getting a much better deal because it lasts a lifetime.”
Century Slate, in Durham, N.C., is a certified installer of both VM Zinc and Rheinzink. “Zinc is a malleable metal and can therefore be more easily shaped than steel,” says Mike Tenoever, president. “But you have to be careful when you are working with zinc, and it must be properly vented or have a protected underside to prevent corrosion.”
Having said that, the payoff, according to Tenoever, is that zinc looks amazing and is long lasting. “It has the warmth and depth of copper but in a uniform gray color. You can purchase mill finish, warm gray or black. The combination of colors can create a unique and lasting look,” he says. “I am in the planning stages with an architect for my own house that I am building. I am going to do the outside walls and roof in the three colors of zinc and a small amount of slate.”
The Green Factor
A contractor installing a material on his own house should be ringing endorsement enough, but maybe you need further convincing about zinc. Well, how about the fact that zinc is good for the environment?“Zinc is certainly green in the sense that it lasts a long time,” says Lowy. But more importantly, zinc is recyclable. “We use over one third recycled material,” he says. “Also, not only is zinc nontoxic, but it is also good for you — the body actually requires it. Water run-off isn’t tainted.”
Remember that you are used to zinc in your multivitamins and sunscreen, so is it really such a stretch to envision it on your next big roofing project?