I once owned a particular cell phone for four years and by the time I finally gave in and upgraded, my friends and family were referring to it as “the Bat Phone.” It is the same with computers and sometimes even cars: The week after you buy one, it is totally out of style and uncool! This would never happen, say, with a copper or terne roof. Put one on your home or office building, and your friends won’t dare refer to it as “The Bat Cave.” Metal has long been a part of history and for good reason: classy looks and durability.
Revolutionary Copper
There is no question that a company has class if it was started by Paul Revere — the Revolutionary War patriot who was also a renowned silversmith. Revere Copper Products, Rome, N.Y., celebrated its 200th anniversary in 2001. Roofing Contractor reported on this event at the time, but it’s such a great story it’s worth telling again.With operations in Rome, N.Y. and New Bedford, Mass., Revere Copper holds the distinction of having one of the 10 oldest continuous brand names in the United States. “There are other older companies in the financial and agricultural markets, but we are the oldest continuous manufacturing company in the United States,” explains David Hunt, manager of Architectural Services for Revere Copper.
Paul Revere had followed a family tradition and by the age of 22 was a master silversmith. During the revolution, his industrial activities included supplying the army with powder and cannon. Following the war, he turned to the production of ship fittings and church bells, which to this point were imported from England. According to Revere Copper, many are still in use.
“Revere had 13 children and needed to tend to them after the war,” says Hunt. He explains that the states did not have the copper rolling capacity needed for cladding war ships because the British thought of their colonies as places to get raw materials and sell finished goods, but did not encourage manufacturing. And after the war, “The Brits were not too keen on supplying copper!” says Hunt.
In 1801, at the age of 65, Revere established the first copper rolling mill in the United States in Canton, Mass. Among the first orders were $10,000 worth of copper sheathing for the navy and 7,675 pounds of copper sheets for the new State House in Boston. Revere’s son Joseph, who was his partner in the business, went to England, Wales, France and Denmark to work as an apprentice and bring back technological skill and knowledge. This firm became known as Revere & Son.
Noteworthy transactions for the new company included copper sheets for the U.S.S. Constitution (also known as “Old Ironsides”), copper plates for Robert Fulton’s first steamboats and guns for the army and navy in the Civil War.
In 1900, the Revere Copper Co. merged with two others located in Tauton and New Bedford, Mass. In 1928, this company merged with several others, including Rome Brass and Copper Co. Members of the Revere family have served in management functions until the last associated with the business retired in 1996.
Over the years, other high-profile profile places furnished with Revere Copper include the White House, the United Nations building and the Statue of Liberty. And here’s a fun historical fact: In the mid 1990s, when the British government was constructing an expansion on the existing Parliament building, the architects called for a copper roof with specifications that were very difficult to come by. Yes, you guessed it, in an ironic twist of fate, Revere Copper was the only company in the world that could meet the architects’ requirements.
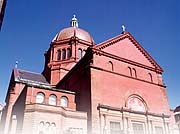
Products Then and Now
Back in the day, you’d have to wait 15 to 20 years for your copper roof to achieve its desired, natural green patina. Now, however, Revere offers customers EverGreen Pre-Patinated Architectural Copper, which shares the self-healing, low-maintenance characteristics of naturally patinated copper. Revere FreedomGray is standard architectural sheet copper coated on both sides with a patented tin-zinc alloy. For homeowners who want a piece of the action, there are Bennington copper shingles.Re-roofing History
According to Hunt, the Massachusetts State House, originally done with Revere copper, has been repaired several times and may or may not still have some of the original material. Christ Church in Philadelphia had a copper roof installed, probably around 1737. “That roof lasted well over 200 years,” says Hunt. “By this time there were problems with the flashing, so the roof was replaced with Revere Copper back in the mid 60s.” Other historic buildings that have been restored with Revere Copper include King’s Chapel in Boston, originally roofed in 1754; and the State House in Newport, R.I., from 1776. “Those jobs would have been done originally with offshore metal,” Hunt explains. “Another historic metal roof is First Scots Presbyterian Church in Charleston, S.C., which was built before the Civil War. It had a tin roof that was replaced with Revere Copper.” Hunt says this was considered historically acceptable.The Right Tools for the Job
When asked how installation techniques have changed over the years, Hunt answers, “The biggest difference came with the introduction of the portable pan forming machine in about 1978 by ESE Machines. Also, the AutoBrake was significant. Hand tools are basically the same. While they may be made with stronger alloys and plastic grips, you can basically pull out a catalog from 1900 and the tools would be the same.”A recent job where the use of both old and new tools was showcased involved replacing the copper dome at Quincy Market in Boston. The 170-year-old market served as Boston’s wholesale food distribution center until the 1960s. The original Revere Copper roof dates back to the early 1800s. Gilbert & Becker Co. Inc., Dorchester, Mass., a full service union roofing contractor established in 1947, was charged with the reroofing job. The company specializes in slate, copper and historical restoration.
The crew from Gilbert & Becker removed the old roofing from the approximately 30-square eliptical dome. “We didn’t duplicate what was there,” says owner Alex Alpert. “The first roof was all over the place. The horizontal and vertical seams were not lined up.”
In an example of how modern tools have indeed aided contemporary metal roofing, Alpert explains, “We laid out the lines with a laser beam at night. We used a tool that drywallers use — a self-leveling beam that spins and creates a red line. We then trace the line and create the panels during the day.”
But some things never change. For creating the panels and the actual installation process, Gilbert & Becker had to use hand tools to form the 20-ounce Revere copper. “This job was extremely challenging,” says Alpert. “Normally we would fabricate panels in the shop. But for this, everything had to be done on site, by hand — they were flat-seamed panels. And because it was elliptical, no two panels were the same size.” The project took eight workers four months to complete. Alpert says that the tools and equipment necessary for this type of work aren’t made anymore and his company gets what it needs — including antique hand-cranked turning machines and hand brakes — at auctions and from other companies that go out of business.
History Repeats Itself
Follansbee Steel, Follansbee, W.V., is another company with staying power, tracing its history back to the early 1800s. First owned and operated by James Park, the company’s products included block tin, ingot copper, antimony, sheet zinc, sheet iron and tin-plated carbon steel.Ownership of the facility transferred from James Park to James Scott, and eventually was purchased by brothers John and Robert Follansbee, who then constructed a larger facility. The 1902 opening of the Follansbee Steel plant gave rise to the establishment of the city of Follansbee. Follansbee Steel has occupied its present manufacturing location for over 100 years. In 1954, Follansbee Steel was purchased by The Louis Berkman Co., and all basic steel production operations were eventually sold to Wheeling Steel. The coating lines and a sheet metal specialty operation were retained.
Though much remains the same, products and technology continue to develop. Follansbee now uses state-of-the art “air knife systems” in place of antiquated roll coating systems and has introduced modern alloys to the concept of the original tin roof.
Follansbee markets Terne II as a new and improved version of the historic terne metal. The company contends that while it retains all the qualities of the original, Terne II has improved capability for resisting corrosion. With the new material, however, Follansbee advises painting as soon as conditions permit. Oxide formation is slower than with the original terne. Terne II is coated with Follansbee’s ZT alloy, a combination of zinc and tin. This coating is designed not only as a barrier but also to be anodic to the steel substrate and reduce the potential for oxidation before painting.
Follansbee also offers KlassicKolors, a Terne II roofing sheet prepainted with Valspar’s Floropon SR Solor reflective paint coatings. The product is available in 20 colors as well as custom-formulated hues. A primary objective in creating the color selection was to maintain the oxide hues that have characterized terne/tin roofs since colonial times.
And finally, Follansbee offers TCS II, which is 304 architectural stainless steel, coated with the ZT alloy. The alloy is reactive to oxygen in the atmosphere, forming a gray surface oxide with exposure to the environment. According to the company, original TCS, as well as other lead alloy coatings traditionally used for metal roofing, were dependant on sulfur compounds in the air to form a gray surface patina. Newer clean-air policies have resulted in a reduction in sulfur emissions and acid rain, which have rendered the weathering of lead and lead alloys unpredictable. Follansbee contends that TCS II affords “aesthetic predictability.”
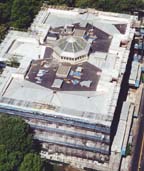
A Terne for the Better
For some insight into using the new terne products to replace the old, we spoke to Jack Waite from John G. Waite Architects, Albany, N.Y. The firm has done extensive research on historic roofs, including writing a handbook on the subject for the National Parks Service (Metals in America’s Historic Buildings: Uses and Preservation Treatments, published by the U.S. Government Printing Office).“We’ve restored probably two or three dozen historic buildings with terne,” says Waite. “We’ve gone to England where tin plate was made in the 18th century. They used slabs of wrought iron with tin/terne coating. The closest thing to historic terne is made with stainless steel.”
Waite Architects has also done research on pan sizes. “The 10- by 14-inch modules go back to medieval times,” Waite explains. “The 19th century saw increases up to 14 by 20 and 20 by 28 — always on a 10-by-14 module. By looking at the size you can tell roughly when it was put on.”
One recent restoration project for Waite Architects was the Tweed Courthouse in New York City, a terne-coated corrugated iron roof from the 1870s. The building had not been used as a courthouse for 30 years, though it housed various city agencies. It was first made a city landmark in 1984 and then a national historical landmark. Most recently, Tweed Courthouse served as a cultural facility until the current administration, under Mayor Michael Bloomberg, moved in the city’s department of education.
According to Waite, the original roof managed to last until the 1970s even though it was terribly maintained. It was then covered with asphalt shingles, but they failed quickly. In short, the “Roof was a mess when we got it,” says Waite. Crews had to tear off material down to the roof framing because the roof had leaked so badly people could literally step through it. “We had new terne-coated stainless steel installed in historic sizes,” says Waite. The Follansbee product had to be custom-rolled by a metal fabricator.
After this though, installers used modern techniques. “The courthouse had to look historically accurate but be weather-tight,” Waite explains. The original corrugated sheets were designed to be installed by carpenters not metal workers, and they were nailed down. This time around, crews used modern stainless steel fasteners to avoid pull out and roof failure.
Mr. Jefferson’s Roofing System
Whereas the Tweed Courthouse used modern material and equipment, other projects in which Waite Architects has been involved are interesting for their use of original tools and technology. One such undertaking involved replacing homes owned by Thomas Jefferson in addition to some of his buildings at the University of Virginia, built in the early 1800s.The firm came across this project while doing historic structure reports at UVA. “While we were researching one of the old buildings, the maintenance staff told us about a leak on another structure,” Waite explains. That building had slate that needed to be replaced, but, “Underneath we saw something we had never seen: tin-plate pans that were half of a 10-by-14 sheet, locked on the sides, put on like shingles,” he says. It was Jefferson’s original roof that had lasted until this day.
According to Waite’s research, Jefferson had intended the roofs to be slate — if he could get the material from a specific quarry and have a particular installer do the job. When this did not work out, Jefferson remembered that he saw tin plate on a grain market in Paris. So he ordered tin plate from Wales and found two artisans from Philadelphia to do the installation. Alas, the craftsmen were wanted by the authorities and extradited to Delaware before they could do the work.
Undaunted, Jefferson devised a system to install the plates, “Almost the way you would install wood shingles,” says Waite. Jefferson had the roofs installed on the buildings at UVA and his home at Monticello, as well as his getaway retreat called Poplar Forest.
Jefferson was very proud of the work and, according to Waite, it was impressive. But in a hard driving rain, capillary action caused extensive leaking. “So, when we came back 175 years later to replace the roofs, we used an underlayment,” says Waite. In all other respects, however, the firm used Jefferson’s system to replicate the original roof and trained the university’s crew to install it. “We did four roofs in this way,” says Waite. “We used terne-coated stainless steel. There was no soldering at all — Jefferson didn’t use any. We had dry seams, though we used some white lead used as a sealant.”
Waite adds, “It may not be the best way to install such a roof, but it’s the way he did it.” In addition, “When the installation process started, we looked at the first course and saw that it was not even. When we looked at Jefferson’s house, we saw the same thing.” Historical evidence suggests that Jefferson was unhappy with that too! Nonetheless, “We also encapsulated one of the original roofs so years from now people can still see it.”