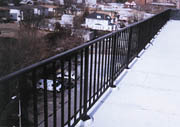
A longtime area company, All-Star was the successful bidder to reroof two sister buildings in Far Rockaway, N.Y. The identical apartment buildings, Ocean View Apartments I and II, are located within a city block of each other. The roof of each building covers 24,000 square feet. Along the perimeter of each were 150 steel pipe penetrations that supported safety rails.
Using conventional pitch pockets to seal the roof penetrations on Ocean View I proved to be labor intensive, and past experience had shown pitch pans were a frequent source of leaks. Thus, the twin buildings allowed All-Star to compare the installation of conventional pitch pans with a newer penetration sealing system, the Chem Curb, developed by Chem Link Inc., Kalamazoo, Mich.
Both jobs involved tear-off of the existing roof and replacement with a new Firestone APP 20-year modified membrane system. The new roof was composed of iso board insulation, a 28-pound fiberglass base sheet, an APP-160 smooth-surface modified cap sheet and a white, granulated APP-180 modified cap sheet.
According to Ronald G. Taylor, All-Star’s president, the work on Ocean View I involved fabricating the aluminum pitch pockets off site. They were then secured in place with screws. Workers next had to prime, torch apply two plies of flashing, and then pour in non-shrinking grout, followed by asphalt cement. Finally, crews spread white roofing granules for aesthetic reasons.
“After we completed work on building one, one of our suppliers, H. Verby & Co., told us about the ChemCurb system,” Taylor says. “We decided to try this product to seal the 150 roof penetrations on the sister apartment, 249 Ocean View II. After carefully checking out the specs, we felt we had a unique opportunity to compare total installation costs. Another determining factor was the 10-year product warranty the new system offered, whereas the old style offers no warranty.”
Using the product to seal the roof penetrations on building two, All-Star cut the seven-step pitch pocket method down to three steps. “I figure we saved at least an hour per penetration in labor costs,” Taylor says. “A savings of at least 150 man hours, perhaps a little more.”
As for material costs, “When you add up the cost of aluminum, primer, APP-160 smooth, APP-180 granulated flashing, roofing granules and propane required for a pitch pocket and compare it to the cost of the ChemCurbs, with their adhesive and pourable sealant, we probably saved on material cost as well,” Taylor continues. “We saved almost $34 per roof penetration. Total savings were about $5,000, enabling us to pass the savings on to our customer.”
It’s not often that a contractor can see cost comparisons so clearly in the field, but being able to pass along a $5,000 savings to the customer is something to pay attention to.