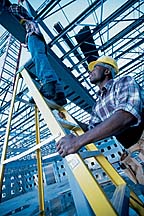
In reality, budget and schedule often supersede safety concerns. On the multi-employer construction sites I've audited, hazard communication is Spartan within any one company and all but non-existent between prime and subcontractors. There might be weekly job meetings scheduled, but attendance is usually weak across the board. Few, if any, cross-contract safety issues are thoroughly reviewed and resolved in detail. It just seems that the written, site-specific safety and emergency action plans for every contractor are far from a project-wide reality. Everyone admits to gaps in safety policies, but no one takes the time or expense to upgrade policy, purchase equipment or train personnel to correct the deficiencies.
These communication failures primarily occur between different contractors who are simultaneously on the site but unrelated by any written contract. Those employers who are parallel in the contract diagram seldom discuss their operations or schedules in any detail.
The fact of the matter remains that until faced with either a serious OSHA violation, a costly worker's compensation claim or a bid denial by a prime contractor due to a high experience modification rate, not much will change the safety course of a contractor. It is prudent for every contractor on a multi-employer worksite to understand the potential for costly OSHA co-violations. Generally, only enforcement promotes compliance.
In December 1999, OSHA issued the most recent revision to its Field Inspection Reference Manual by way of CPL 2.103 (issued Sept. 26, 1994), which replaces (and clarifies) its previous interpretation, Chapter III, Paragraph C.6, concerning OSHA's multi-employer citation policy. Issued by the directorate of construction to all national, regional and area OSHA offices more than five years ago, this CPL described the policy changes to be applied by both state and federal compliance officers for safety and health prior to citing a contractor on a multi-employer worksite.
The CPL also gave some examples of when, based on relevant inspection data and facts, citations should or should not be issued to expose, create, correct or control employers. In any case, the 5(a)(1) General Duty Clause of the Occupational Safety and Health Act (1970) still remains in effect, requiring the employer to provide all employees a type and place of work that is "free from recognized hazards that are causing or are likely to cause death or serious physical harm to his (her) employees."
Once an OSHA compliance officer arrives on a multi-employer site, he introduces himself to the prime contractor (who has over-riding control of the construction project) and then to that specific contractor/employer who was reported in violation by an anonymous worker. The compliance officer will then conduct a pre-inspection meeting with that employer and his designated employee representative in which the safety issues to be inspected are discussed. Once the physical inspection is under way, the compliance officer initiates a process to assess workplace conditions and determine whether more than one employer is to be cited. It is broken down according to the role that each employer is determined to fill on the job and the company's working relationship to the existing or potential on-site hazard.
1. Creating Employer
Step 1 - Identification:Is this employer the one whose employees actually caused a hazardous condition(s) to exist, or potentially exist, on site, which violates a specific construction standard?Step 2 - Action Taken:No employer is allowed to create an unsafe or unhealthy workplace condition exposing one or more employees to hazards that violate any OSHA standard or the General Duty Clause, even if the only employees exposed to such hazards work for another employer.Example:Prime Contractor A hires Subcontractor B to install finish roofing on its newly framed condominium. Contractor A's non-certified, untrained forklift operator strikes and damages the scaffolding from which Subcontractor B is working. Subcontractor B evacuates the damaged scaffolding and secures the area with danger tape until the scaffolding can be dismantled and replaced.Analysis:The compliance officer may determine that Prime Contractor A is the Creating Employer as his powered industrial truck program did not sufficiently train and evaluate his forklift operator.2. Exposing Employer
Step 1 - Identification:Is this employer one whose own employees are directly or indirectly exposed to the hazard or hazards identified in the inspection? A hazardous exposure is determined to be either a health- or safety-related issue depending on the probability of occurrence vs. the severity of the effects.Step 2 - Action Taken:If the exposing employer actually created the hazardous condition, he is citable for the violation as a creating employer.
If the violation was created by another employer, the exposing employer may be cited if:
It was reasonable to assume or he admitted to knowing of the hazard.
He failed to exercise due diligence in initially observing the hazard. If the exposing employer lacks the authority to be a correcting employer he may be cited if he fails to:
Ask the creating and/or controlling employer to correct the hazard.
Inform his employees of the hazardous condition.
Take "reasonable alternative protective measures" or remove his employees from imminent danger.
Example: Roofing Contractor A had no direct contractual relationship with Painting Contractor B on the project. The Host Employer (owner) provided scaffolding around the roof edge and the contracted services of its competent person for supported scaffold, as part of its painting contract with Contractor B, who removed some guardrails creating a scaffolding violation. The Host Employer gives Roofing Contractor A temporary scaffold access to the roof in order to perform contracted repairs. Roofing Contractor A asked Painting Contractor B to replace the guardrails before his employees accessed the scaffolding, but Contractor B refused. Roofing Contractor A informed the Host Employer (who owned and installed the scaffolding) of the violation but the Host Employer did nothing to correct the hazard. Roofing Contractor A then implemented personal fall arrest systems for each of its employees, while Painting Contractor B continued work on the scaffolding without fall protection.
Analysis: Painting Contractor B is an exposing employer because his employees have removed guardrails and not installed PFAS, and he is therefore citable for the scaffold violation. Roofing Contractor A asked that Contractor B correct the scaffold fall hazard, and, when no guardrails were replaced, implemented his own compliant fall protection methods in compliance with the scaffold and fall protection standards. Contractor B was then no longer considered an exposing employer and was not considered citable. The Host Employer had no employees of its own exposed to the hazardous condition. The Host Employer was not considered the creating employer, because its employees had originally erected standard-compliant scaffolding.
3. Correcting Employer
Step 1 - Identification:Is this employer one who is engaged in a common undertaking, on the same worksite, as the exposing employer and is responsible for correcting a hazard? This usually involves an employer who is responsible for installing/maintaining safety equipment or systems.Step 2 - Action Taken:The correcting employer must continually exercise reasonable care in preventing and/or discovering OSHA standard violations and thereby meet its obligation to correct the condition until the hazard is no longer exposed to any employees.Example:In continuing the previous example, the Host Employer is responsible for the installation, maintenance and removal of the scaffolding, as well as the competent person, in its contract with Painting Contractor B. The Host Employer's competent person should have reasonably detected the missing guardrails and taken "prompt corrective measures" to either replace them or implement some other compliant means of fall protection for all exposed employees (Contractors A and B).Analysis:The Host Employer is therefore considered the Correcting Employer and is citable for not implementing fall protection or guardrails for Painting Contractor B in compliance with the scaffold standard. While the Host Employer has no contractual obligation to provide scaffolding or competent person services to Roofing Contractor A, it did give it permissible access to the roof on the scaffolding. Therefore, Roofing Contractor A is responsible for providing its own competent person, who then inspected the scaffolding and found the missing guardrails and implemented an alternative fall protection system for its employees. Roofing Contractor A is considered a Correcting Employer for its own potentially exposed employees and, therefore, is not citable for a violation.4. Controlling Employer
Step 1 -Identification:Is this employer one who has general supervisory authority over the worksite? This may include the power and ability to control safety and health violations or else require others to correct hazardous conditions by means of either specific contract language stipulating health and safety duties and responsibilities; or general exercise or assumed practice of control in matters of job-site safety.Step 2 - Action Taken:The Controlling Employer must continually exercise reasonable care in preventing and/or discovering OSHA standard violations. The extent of prevention measures undertaken by a Controlling Employer in order to satisfy his duty of "reasonable care" is considered less than that of the Correcting Employer. The Controlling Employer is often less experienced and qualified as the employer it contracted. The following "reasonable care" items may determine how extensive and frequent the Controlling Employer's site inspections shall be:1. Size and scope of the job or project (project operations plan and critical path schedules).
2. Nature of the work and the frequency of existing/potential hazards (Job Safety Analysis). 3. Knowledge of the safety expertise and construction experience of the Exposed Employer. 4. History of the Exposed Employer's safety violations and Experience Modification Rate. 5. Ability of the Exposed Employer to self-audit and correct to high level of compliance. 6. Strong indications that the Exposed Employer is consistently implementing his own corporate safety and health program. 7. Examples of enforcement, accident analysis, safety meetings and initial/refresher training.
The compliance officer will initially identify the various contractors on a job site during the opening conference phase of the inspection. The host employer, prime contractor or construction manager will understand the contract relationships between all of the other contractors. Every construction project, from a single-family residence to a power generation plant, may be graphically displayed as a pyramid with the Controlling Employer at the top. Prime contractors and subcontractors may be aligned below by their contract obligations and direction of payment. When the compliance officer evaluates whether the Controlling Employer has exercised "reasonable care" he may consider the following:
1. How often does he conduct periodic inspections? Are they regularly scheduled? Are they random? Is the frequency appropriate for the hazards observed?
2. What means are used to determine if employees have been exposed to a hazard? 3. What "prompt corrective measures" are called for when a hazard has been observed (engineering, administrative or PPE controls)? 4. How does he enforce compliance from other employers? Is the enforcement graduated? Is it effective? Is there any follow-up inspection and analysis?
It is important to understand the method that the compliance officer will use to identify who is responsible for job-site safety and health. While at first glance, there may appear to be more than one Controlling Employer, it is only by investigating the contract language that the contractor in actual control may be identified. There are five major methods for OSHA to identify the Controlling Employers:
1. Control by Established Contract: This employer may be identified in a specific clause in the written contract. It calls out his duty and/or right to implement job-site safety and health provisions among all the signatories to the contract. They must be capable of either preventing the conditions leading up to the hazard and correcting the violation or else designate another party to perform the abatement and correction. The contract should clearly stipulate a graduated enforcement program and clearly define appropriate contract penalties. There also must be a reasonable means of evaluating the effectiveness of both the safety and health program to be enforced and the enforcement of its policies.
2. Control by Combination of Other Contract Rights: Where no other specific written contract authority is granted, the Controlling Contractor may be designated by a combination of other contract rights. An employer may still be considered a Controlling Contractor even when the contract states he is NOT so designated. In order to be assumed controlling the employer must maintain a broad set of on-site responsibilities, including a combination of miscellaneous contract rights involving most aspects of the job. His obligations must imply a responsibility of general safety when such obligations are not assigned to anyone else in the contract. Having the authority to resolve disputes between contractors, set work schedules and determine job sequencing are likely to directly affect job-site safety.
3. Architects, Engineers and Project Managers: These contract entities may be considered Controlling Employers only if the scope of their on-site project management duties encompass safety and health policies. The American Institute of Architects has developed a boilerplate construction contract that contains a safety and health clause.
4. Control Without Explicit Contractual Authority: Sometimes there are no explicit contractor rights with respect to safety and health. It is still possible to be a Controlling Employer if, in practice, the contractor appears to conduct broad control over various contractors and subcontractors on the site during particular phases of construction. The compliance officer will confer with the legal department of the regional OSHA office before making a final identification.
5. Multiple Roles: Every employer on a construction project is minimally responsible for the health, safety, workmanship and productivity of all of his employees. It is possible for any contractor on a multi-employer site to be identified by a compliance officer as a combination of Exposing, Creating, Correcting or Controlling Employer. The inspector will always consider the exposing status first before evaluating any contractor for others simultaneous obligations. Next, the Creating Employer status is assigned to one (or more) contractors on site. The Correcting Employer status is identified as valid if they are duly authorized in some contract language. The Controlling Employer status is considered last as it is often the most difficult to assign.
Example: In continuing the previous example, the Host Employer is responsible for the installation, maintenance and removal of the scaffolding as well as providing the competent person in its contract with Painting Contractor B. The contract language clearly defines the Host Employer as the Controlling Employer.
Analysis: The Host Employer had the obligation of Control Established by Contract. His competent person should have reasonably detected the missing guardrails and taken "prompt corrective measures" to either replace them or implement some other compliant means of fall protection for all exposed employees (Contractors A and B). As no hazard analysis or control measures were taken, the Host Employer may also be cited for this violation.
Conclusion
Without a doubt, multi-employer sites are tough places to work. A competent person should always conduct safety and health evaluations of your specific work during the pre-bid phase of the project. Consider whether there is sufficient material, labor and equipment provided at appropriate times for establishing safe and healthy working conditions throughout substantial completion. Keep in mind that all potential and existing hazards can be identified according to time/place coordinates. Any additional time and effort you commit to analyze the on-site relationships of all of the contract employers before the work begins could protect you from potential OSHA violations.Creating a critical path schedule (time) and conducting a job safety analysis (place) for the proposed work will help you clearly understand your contracted obligations to the prime and subcontractors. Projecting the potential scope of work of other related and unrelated contractors during your duration on site will also help identify the Exposing, Causing, Correcting and Controlling employers. This valuable, pre-bid and pre-construction analysis is meant to help prepare you for the potentially serious hazards awaiting you on every multi-employer work site.