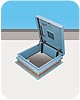
Hatches for high-security applications can be manufactured from heavier gauge materials and modified with a number of options for enhanced security, including deadlocks and bullet-resistant windows.
Roof hatches are frequently used to provide safe and convenient access to and from rooftop areas in commercial buildings. These products allow service personnel to gain access to the roof for maintenance and facilitate the installation or removal of large pieces of equipment into or out of a building.
This article will provide a general overview of roof hatches and will focus on the variety of hatches and options available. It will also address the specification process and some common roof hatch modifications that may be required for specific applications.
Roof Hatches 101
Roof hatches are horizontal doors that cover roof openings and provide access by means of an interior ladder, ship stair or service stair. The type and size of a structure usually determines the method of egress required. A manufacturing facility with a high ceiling, for example, typically requires a ladder to access the roof, whereas an office building or school might have a traditional set of stairs or a ship stair leading to the roof level. Other common applications for roof hatches include factories, office buildings, shopping centers, storage facilities, and non-residential buildings that require access to the roof area.
There are a variety of roof hatches available to accommodate the access requirements of any commercial building. When selecting a roof hatch, a number of factors should be considered, including the purpose of the hatch, whether it’s a new or retrofit application, the type of a facility where it will be installed, and finally the product cost.
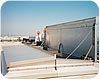
Equipment access hatches are usually specified as double-cover models that are custom manufactured to specific size requirements.
Determining if a hatch will be used to simply gain access to the roof or if it will serve as a means of entry for large pieces of equipment can help determine the size of the hatch required. If a hatch is for personnel access only, a small, single-cover model in conjunction with a fixed ladder, ship or service stair can often be specified. The frequency and reason individuals need to access the roof area can also impact the hatch size; for example, a larger hatch with ship or service stair will enable workers to carry large tools or parts onto the roof for service.
Equipment access hatches are available in larger sizes and are generally specified as double-cover models that are custom manufactured to specific size requirements. The type and dimensions of the equipment will determine the size of the roof hatch required. It is important to contact the roof hatch manufacturer to verify the hatch’s hardware locations and clear opening. Depending on the application, custom hardware may be required. A hatch designed to install a Magnetic Resonance Imaging (MRI) machine in a hospital, as an example, will need to be fabricated with non-magnetic hardware.
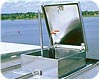
For standing seam metal roofs, curbs can also be modified to allow the hatch to sit directly on a metal roof without a job-built curb.
Most roof hatches are designed to be installed on a new roof, while some applications will require replacing an old or damaged hatch. A low-profile replacement hatch is ideal for retrofit applications. These hatches can cap over an existing hatch curb, eliminating the need to replace roofing material. Once the old hatch cover is removed, the new, low-profile curb simply mounts directly onto the existing curb. A flanged design and full apron ensure a watertight installation.
Type of Facility
The facility where the hatch will be installed can also influence product selection. High-security applications, dark manufacturing or storage facilities, highly corrosive settings or projects requiring special aesthetic considerations will benefit from hatches that are manufactured to address the specific needs of these environments.
High-security applications such as prisons, banks, pharmacies and embassies require all entrances and exits, including roof openings, to be protected from unauthorized access. In such cases, hatches can be manufactured from heavier gauge materials and modified with a number of options for enhanced security. Options typically include gun ports, bullet-resistant view windows and deadlocks.
Skylights can often be found in commercial buildings. Besides serving an aesthetic function, they illuminate dark workspaces in manufacturing and industrial facilities, reducing energy costs. Selecting a hatch with a polycarbonate dome cover will provide the added benefits of a skylight, allowing natural daylight into a building and creating a more pleasant working environment below.
For highly corrosive environments such as chemical plants or in coastal areas with extreme weather conditions, hatches should be manufactured of aluminum or stainless steel for the highest level of corrosion resistance. Copper roof hatches can be used to match the aesthetics of heritage projects and for buildings located in historical districts.

There are a variety of roof hatches available to accommodate the access requirements of any commercial building.
Hatches made of galvanized steel are most commonly specified, primarily from a cost perspective. They provide a basic degree of corrosion resistance and are typically supplied with a primer paint finish. Aluminum hatches, commonly supplied with a mill finish, are slightly more expensive than galvanized steel and require little or no maintenance. Additionally, they offer a higher level of corrosion resistance, which is especially important in coastal areas. Stainless steel and copper products, used for unique applications, are the most expensive options. Hatches fabricated to meet unique size requirements generally carry a price premium.
Selecting a High-Quality Roof Hatch
In the roof hatch selection process, contractors should also consider general design elements in order to select a hatch that will provide a safe means of rooftop access and trouble-free service for their customers. These factors include ease of operation, energy efficiency, and weather-tightness.
Ease of operation is one of the key design elements to consider when selecting a roof hatch. Maintenance and facility staff members need to be able to open the hatch cover upward from inside while standing on a ladder or stairs with, more often than not, tools in hand. The hatch should therefore be designed with uniform lift assistance to ensure smooth, easy, safe operation so that minimum effort is needed to open or close the hatch.
A mechanical method of lifting the hatch (such as compression springs) should be provided to counterbalance the cover for easy and controlled operation regardless of the cover’s size or weight. The hatch should also include an automatic hold-open arm (or arms) to lock the cover(s) in the open position to ensure it will not slam shut in windy conditions and injure the user of the hatch.
A high-quality roof hatch will help maintain energy performance levels in a building, so it is important to select one with fully welded corners and full insulation in both the cover and curb. Many hatch manufacturers offer insulation options for enhanced thermal performance. In addition to being properly insulated, a quality roof hatch should also feature an overlapping cover design and a full perimeter gasket to ensure complete weather-tightness.
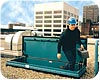
A larger hatch with a service stair enables workers to easily carry large tools or parts onto the roof for service. (Photos courtesy of the Bilco Company.)
Since some applications require custom-fabricated hatches, product manufacturers can typically customize their products without compromising features or performance. Some of the more common modifications are discussed below.
Roof hatches can be supplied with curb liners or fully enclosed curbs for installation on existing curbs. Curbs can also be modified so that they can be installed directly on standing-seam metal roof panels, allowing the hatch to sit directly on a metal roof without a job-built curb or supplied with louvers built into the curb to provide continuous ventilation into a building.
Standard roof hatches offer interior and exterior padlock hasps as an access control feature. For enhanced security, hatches may be designed to include keyed cylinder locks and contact switches that can be wired into a buildings alarm system control panel. Hatches may also be equipped to open remotely with an electric motor or by means of a winch. Both options will provide ventilation of work areas and simplify operation. In addition to the options outlined above, most hatch manufacturers offer special finishes for added corrosion resistance or to allow the hatch to match a building’s exterior. Common finish options include anodized aluminum and paint finishes such as Kynar, Tnemec, and powder coating.
Conclusion
Selecting the appropriate hatch for a specific building or application is a key factor that will impact its service life and required maintenance. In the selection process, contractors should consider the hatch’s intended purpose, whether it’s a new or retrofit installation, type of facility, the location where it will be installed, as well as product cost and aesthetics. When further information is needed, manufacturers and their sales representatives can assist in identifying the product best suited for an individual project.
Report Abusive Comment