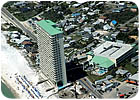
The Celadon beach resort condominiums in Panama City, Fla., feature more than 26,000 square feet of Englert Series 2500 standing seam roofing in patina green atop the 23-story building and on the nearby activities building. (Photo by Blue Yonder Aerial Photography.)
Celadon in Panama City Beach, Fla., was one of the first high-rise condominiums to be designed after the 2004 Florida building codes took effect. The 220-foot-tall structure has 193 one-, two- and three-bedroom units, and it is just yards away from the Atlantic Ocean. Architect Baynes Collins took a page from his school construction projects and instead of choosing a traditional truss structure over the new flat roof opted for a light-gauge retrofit frame and standing seam roof normally used to build over an existing flat roof system. Collins liked the retrofit-type approach because of its flexibility in installation and its proven ability to withstand hurricane-force winds in Florida. He also specified Englert Series 2500 standing seam because of its ability to withstand the effects of pounding winds and rain within 100 yards of the saltwater environment.
More than 26,000 square feet of 18-inch standing seam was used atop the 23-story building and on the nearby activities building, which houses playrooms and a small theater. The color chosen for the 24-gauge, 2-inch mechanically seamed panels was patina green.
The System
The Celadon retroframe on a new flat roof called for a slope purlin system with a metal deck installed over a flat structural concrete building system. The retroframe system was provided by Reroof America Corp. of Tulsa, Okla., and was chosen over a truss system.According to the roofing contractor on the job, Ameritech Roofing of Panama City Beach, Fla., it takes about a third of the time to install, allowing the buildings to be completed two weeks faster than a conventional truss system. Second, the use of a retroframe system eliminates about 40 percent of the cost associated with crane rentals necessary to erect a truss system. Third, the retroframe system is spaced on four-foot centers versus the typical two-feet-on-center spacing for a truss system, providing a substantial amount of rooftop storage space. And fourth, the retroframe system requires 50 percent fewer fasteners than a truss system, eliminating a lot of material costs.
The system cut down labor costs as well. In contrast to a truss system, where each form must be installed sequentially, the retrofit system allows a contractor to spread 15 to 20 workers around the roof to work on various sections of the system at one time. The use of the retrofit system also eliminated concerns about installing trusses atop a concrete deck that might not be perfectly flat, a fairly common concern - particularly with concrete poured later in the day. It's difficult to install a truss system if the concrete deck isn't flat or if specifications are off. The retrofit system eliminates concerns that the dimensions of the building envelope might be even slightly different than the dimensions of the specified, prefabricated truss once the structure is being built. If that happens or the building is not perfectly square, the contractor is faced with a difficult challenge of attempting to field-modify trusses that are prefabricated of 16- gauge or 18-gauge galvanized steel.
The Design Process
Overall, these projects - whether new or retrofit - are easy to plan and install. An architectural or engineering firm designs the retrofit roof system utilizing information on structural framing members and structural standing seam roof systems available from various qualified suppliers. The design is usually done with input from the manufacturers of the standing seam roof system.Once the engineering study is finished, a complete workup of all materials including the standing seam roofing is done. The architect uses standardized sections and details with computerized drawings and estimating methods to provide a complete design that meets code requirements and the unique needs of the project.
Collins and Ameritech also developed the same system for the 130-unit Adagio condominium resort project in Blue Mountain Beach, Fla. The project encompasses several four- and five-story condominium buildings just yards from the Atlantic Ocean. And, Collins notes, it didn't cost any more than a flat roof or truss system to add the metal roof.
For more information, visitwww.englertinc.com.
Sidebar: Just the Facts
Project: Celadon Condominiums, Panama City Beach, Fla.Owner: Celadon Beach Development Inc., Mary Ester, Fla.
General contractor: W.G.Yates & Sons Construction Co., Panama City Beach, Fla.
Roofing installer: Ameritech Roofing, Panama City Beach, Fla.
Architect: Collins & Associates, Panama City, Fla.
Material manufacturer: Englert Inc., Perth Amboy, N.J.
Report Abusive Comment